Selecting the right oil tank gasket is crucial for ensuring the seamless operation and long-term durability of your oil storage system. Gaskets, though seemingly insignificant, play a pivotal role in preventing leaks, maintaining system integrity, and enhancing the safety of oil tanks. Recognizing the typical materials and understanding their respective benefits can greatly enhance your ability to make informed decisions when sourcing gaskets.
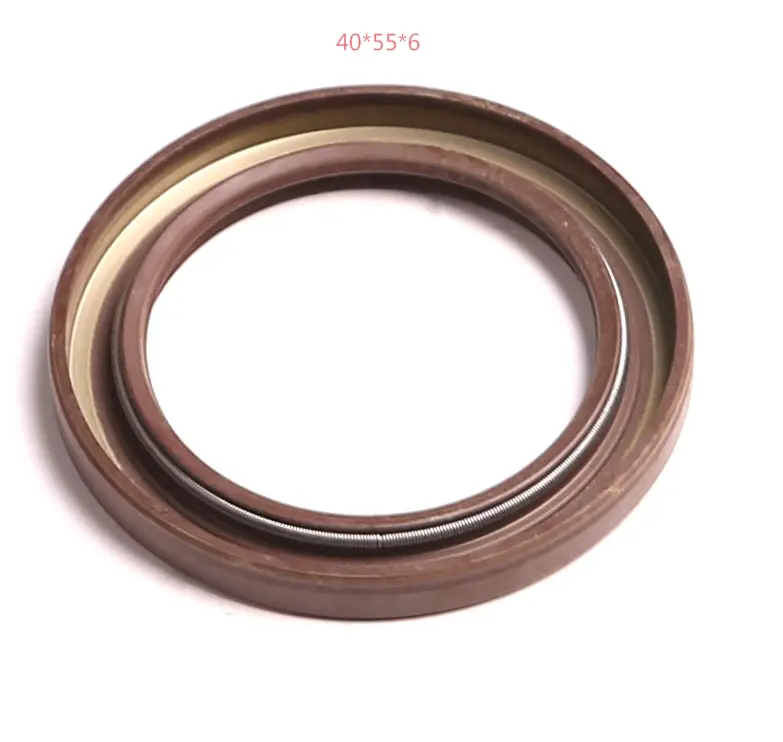
Oil tank gaskets are predominantly crafted from materials like rubber, PTFE (polytetrafluoroethylene), and composite products, each suitable for varying operational conditions. Rubber gaskets, often made from nitrile or neoprene, provide excellent resistance to oil, making them ideal for many industrial applications. Their flexibility and resilience to deformation under pressure also contribute to their widespread use.
PTFE gaskets stand out due to their exceptional chemical resistance and ability to withstand extreme temperatures, which offers great longevity even in the harshest environments. They are often the preferred option in conditions where other gasket types might deteriorate due to aggressive fluids or high temperature variations.
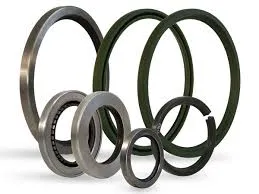
Composite gaskets that blend different materials can strike a balance between performance, durability, and cost. These are particularly effective in high-pressure applications where a single material might not suffice on its own.
Installation practices and regular maintenance are essential elements impacting the effectiveness of oil tank gaskets. Ensuring that gaskets are properly seated during installation minimizes the risk of leaks. Over-tightening fasteners can lead to distortions or damage, compromising the gasket's function. Utilizing torque wrenches guarantees that appropriate pressure is applied, helping maintain gasket integrity over time.
oil tank gasket
Proactive maintenance, including regular inspections, ensures that gaskets remain intact and free from degradation. Schedules should allow for visual inspections and replacements every few years, depending on operational conditions and manufacturer guidelines. Monitoring for signs of wear such as cracking or thinning can avert potential failure, mitigating risks associated with oil leaks — which can lead to environmental damage and significant financial penalties.
It's also vital to employ gaskets from reputable manufacturers. A trusted supplier with accreditation and industry certifications provides assurance of quality and reliability. Their products are usually subjected to rigorous testing, ensuring that they meet industry standards and withstand demanding operational requirements.
Furthermore, considering technological advancements in gasket manufacturing can enhance performance. Recent innovations offer improved sealing capabilities, often with advanced materials that promote longevity and durability. These enhancements reduce the need for frequent replacements, which can translate into significant cost savings over the lifespan of an oil tank.
Lastly, expert consultation can be invaluable. Gasket selection can often be complex, with choices heavily influenced by specific operational criteria — pressure, temperature, chemical compatibility, and environment. Collaborating with engineers or specialists who possess the technical expertise in fluid dynamics and material science can allow for optimal gasket selection, tailored precisely to your application.
In summary, selecting and maintaining the appropriate oil tank gasket involves comprehensive consideration of material properties, installation procedures, and routine checkups, complemented by a commitment to quality and innovation. By making informed decisions supported by expertise and authoritative advice, one not only enhances the operational efficacy of an oil storage system but also upholds safety and compliance standards. With the right approach, the small yet mighty gasket ensures peace of mind, ensuring seamless operation and safeguarding both financial and environmental interests.