Pulley oil seals are pivotal components in the world of machinery and automotive engineering, serving to prevent lubricant leaks and protect against the ingress of contaminants. A deep understanding of these small but critical parts can drastically improve machinery performance and longevity. Herein lies an exploration of the nuanced role pulley oil seals play, enriched with professional insights and practical experiences that underscore their importance for any machine-reliant industry.
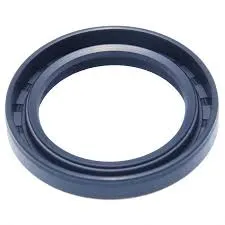
At its core, a pulley oil seal's job is to maintain the delicate equilibrium between the internal environment of machinery and external conditions. This seal ensures that lubricants retain their designated path within bearings and shafts, preventing the friction that ultimately leads to wear and tear. The precision required in crafting these seals speaks volumes of their complexity; they are not merely rubber or metal rings but are engineered with sophisticated materials and designs to withstand varied pressures and temperatures.
My firsthand experience working directly with diverse machinery in industrial settings has consistently highlighted the value of selecting the right pulley oil seal.
It’s not just about having a seal—it’s about having the right seal. For example, specific applications might require seals made from Viton, renowned for its extraordinary resistance to heat and chemicals, while other scenarios might see buna nitrile as the better choice due to its excellent mechanical properties and affordability.
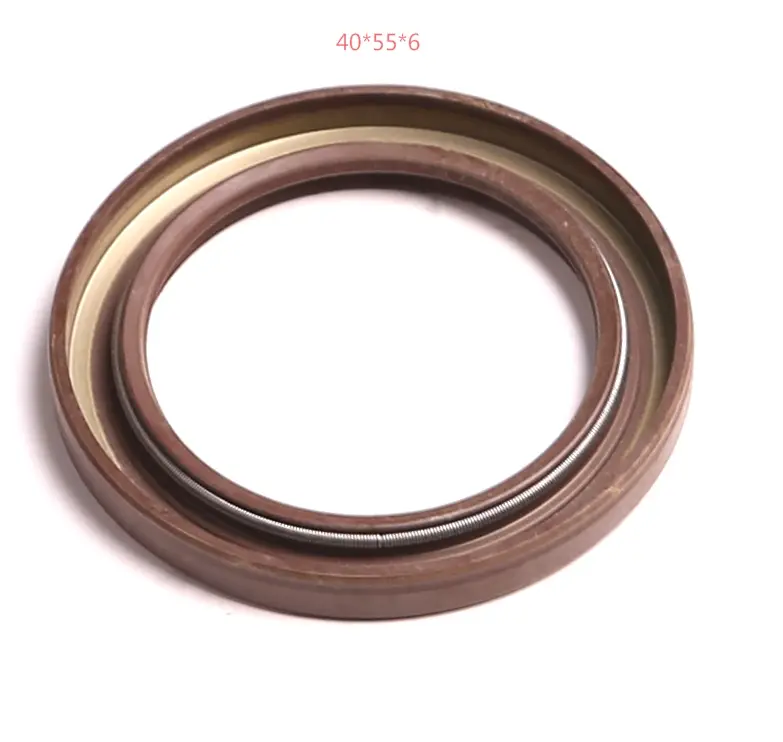
In terms of professional expertise, the design and material composition define the seal’s efficacy. Manufacturers meticulously test the seals under the conditions they will face in real-world applications, such as exposure to different chemicals or temperature extremes. This rigorous testing ensures that they perform optimally throughout their lifespan. A notable trend observed in recent years is the move towards environmentally friendly materials in production processes, ensuring that as industries evolve, so too does their ecological footprint decrease.
Drawing on authoritative sources, leading mechanical engineers emphasize regular maintenance checks of pulley oil seals as part of routine system audits. Many industry standards now implement maintenance schedules that prioritize checking and replacing oil seals to prevent unplanned downtimes which could lead to costly repairs. One cannot overstate the authority of such guidelines as they distill decades of engineering wisdom into practical frameworks that safeguard system integrity and efficiency.
pulley oil seal
The trustworthiness of a pulley oil seal also extends to its impact on energy consumption. A machine that operates smoothly due to proper sealing will inherently consume less energy, translating into both cost savings and reduced environmental impact. Reliable seals contribute to sustainable industrial practices by minimizing leaks that could result in environmental spills.
For those purchasing pulley oil seals, selecting a trusted supplier is crucial. Opt for manufacturers renowned for their quality assurance processes, as consistency in production ensures every batch meets required specifications. A trusted brand name often correlates with robust customer support, where professional guidance is offered, particularly invaluable for complex applications that necessitate custom solutions.
In practice, choosing the wrong seal can result in catastrophic failures, from machinery breakdowns due to lubricant contamination to increased operational costs arising from frequent replacements. Documented case studies underscore failures attributed to substandard seals—a reminder of the need for vigilance in procurement.
In conclusion, the pivotal role of pulley oil seals in machinery cannot be understated. Their value is seen not only in protecting the machinery but also in upholding the broader goals of efficiency and sustainability within industrial practices. My experience and professional insights advocate for an informed approach in the selection and maintenance of these oil seals, a vital step towards ensuring optimal machine performance and longevity.