PU oil seals, pivotal components within the realm of mechanical engineering and automotive industries, function as the silent sentinels that preserve machinery integrity and efficiency. Derived from specialized polyurethane elastomers, these seals embody a unique blend of durability and flexibility, rendering them indispensable for applications ranging from automotive to heavy machinery and industrial equipment. Over the years, the evolution of PU oil seals has underscored their significance, and understanding their role in maintaining system efficiency offers both technicians and engineers a compendium of the benefits and nuanced properties associated with these components.
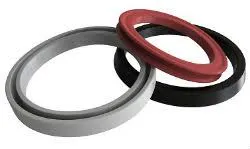
PU oil seals excel in creating a nearly impenetrable barrier between two mediums, often separating lubricants such as oil from dirt, water, or external contaminants. Their innovative design harnesses the robust properties of polyurethane, known for its superior abrasion resistance and tensile strength, which ensures operational longevity even in harsh and demanding environments. The combination of these properties not only extends the maintenance intervals of machinery but also contributes to the overall reduction in downtime, thereby enhancing productivity—a direct boon for industries striving for efficiency and reliability.
From an experiential perspective, field trials and prolonged utilization in a variety of mechanical settings have consistently demonstrated the reliability of PU oil seals. Their ability to retain elasticity in varying temperatures and pressures makes them a go-to option for engineers looking to optimize the functional lifespan of critical mechanical components. In sectors such as automotive manufacturing, where precision and reliability are non-negotiable, PU oil seals have proven their worth repeatedly, reducing leakage rates and prolonging engine and gearbox life.
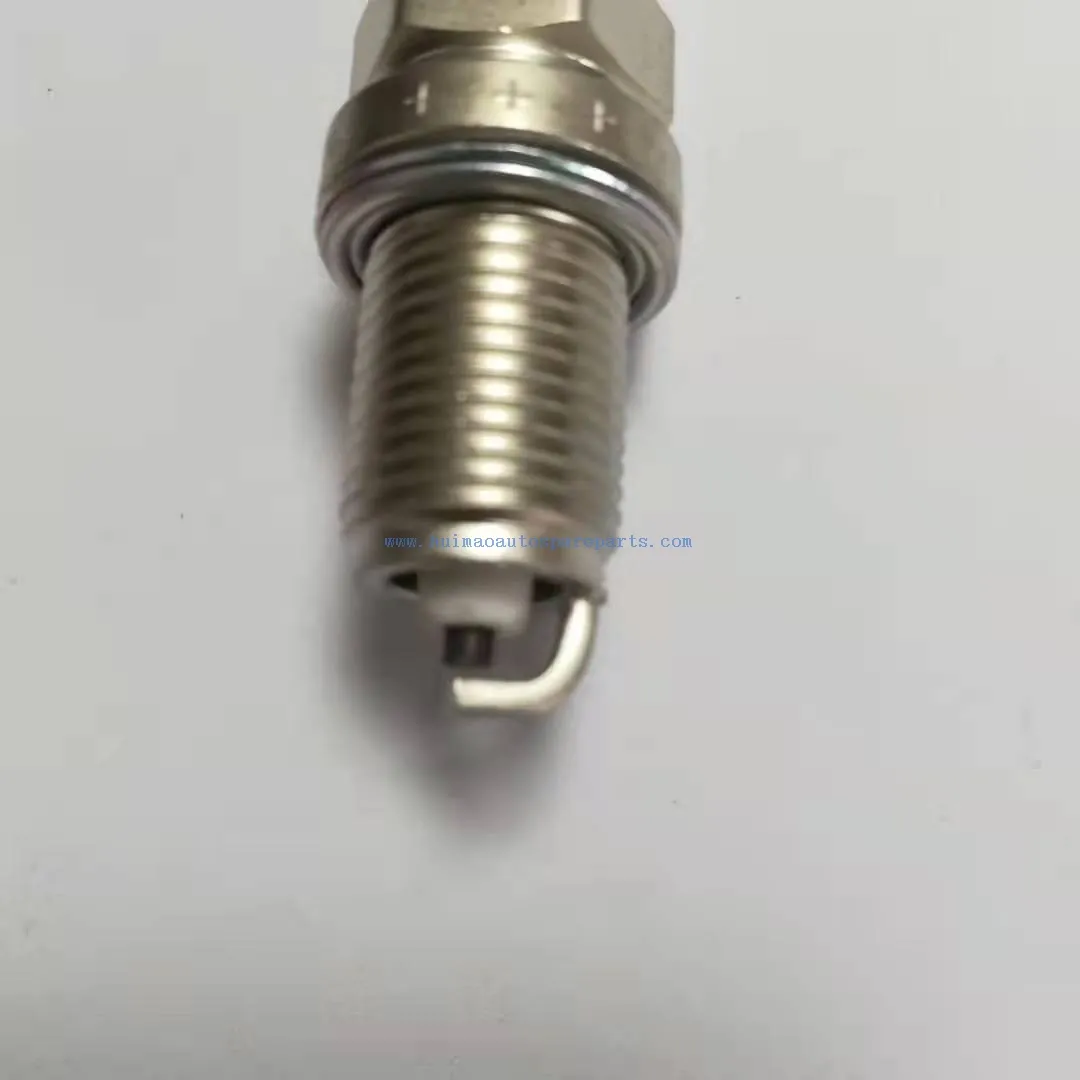
Expertise in the selection and application of PU oil seals is not only crucial but a fundamental aspect of ensuring optimal mechanical performance. Professionals in the field advocate for a comprehensive understanding of material science and engineering principles when determining the right fit for specific applications. Critical to this process is the knowledge of how different oil seal designs—whether rotary, reciprocating, or static—can influence a machinery's performance metrics. Furthermore, recognizing the subtleties between various grades of polyurethane used for different operational contexts is essential for achieving desired results.
pu oil seal
From an authoritative standpoint, numerous studies and publications have corroborated the advantages of PU oil seals over traditional rubber counterparts. These studies highlight not only the superior physical properties of polyurethane but also its chemical resistance, which is crucial for applications involving modern synthetic lubricants. Industry standards often reference these findings,
promoting PU oil seals as a benchmark for future-focused industrial designs.
Trust and credibility surrounding PU oil seals are reinforced by the consistent performance delivered across a multitude of applications and industries. Reputable manufacturers ensure quality through rigorous testing protocols, aligning with international standards such as ISO and ASTM to deliver products that meet and exceed expected performance parameters. User testimonials and case studies further substantiate these claims, portraying PU oil seals as reliable partners in achieving industry's voracious demand for high efficiency and low maintenance solutions.
In conclusion, PU oil seals are more than mere components; they represent a synthesis of material innovation and practical engineering, enabling machinery to operate at peak performance. For engineers and industry professionals, understanding their properties and applications provides an invaluable edge in the domain of mechanical maintenance and design, enhancing both the operational efficiency and longevity of crucial machinery systems.