Radial oil seals, also known as shaft seals, play an indispensable role in a variety of applications by preventing the leakage of fluids along rotating shafts. With the continuous advancement in engineering designs and industrial demands, understanding the intricacies of radial oil seals becomes crucial for any professional involved in machinery maintenance or design.
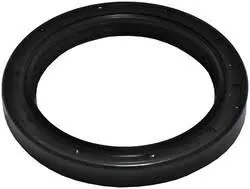
When it comes to experience, radial oil seals stand the test of rigorous conditions, from automotive engines to heavy machinery. These seals, typically made from rubber, metal, or a combination of materials, ensure that lubricants remain in place, which not only improves efficiency but also extends the lifespan of machinery. An industrial case study highlights how a manufacturing plant reduced machinery downtime by 30% by upgrading to high-performance radial oil seals, emphasizing their impact on operational efficiency.
Specializing in radial oil seals unveils a fascinating interplay between material science and engineering precision. A critical factor in the expertise of these seals is understanding the compatibility of seal materials with different fluids and environmental conditions. Nitrile rubber might be ideal for many petroleum-based oils, but for high-temperature applications, fluoropolymer elastomers might be more suitable due to their superior heat resistance. This specialized knowledge ensures the right seal selection, avoiding costly machinery failures.
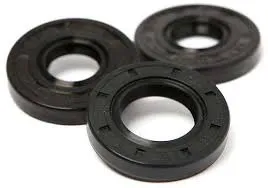
radial oil seal
Authoritativeness in the domain of radial oil seals is reinforced by adherence to rigorous industry standards and compliance. The most respected brands in the market invest heavily in R&D to develop seals that exceed standards like ISO 6194, which prescribes the dimensions and tolerances of shaft seals. Expert recommendations from seasoned engineers often guide the practical choice of seals to match specific industrial requirements, solidifying the credibility of products endorsed by research-driven evaluations.
Trustworthiness is a hallmark of premium radial oil seal manufacturers. Leading companies provide extensive data on the performance and testing of their seals, offering clients the assurance of durability and resilience. A reputable manufacturer shares comprehensive test reports, illustrating seal resilience over thousands of operational hours under simulated conditions identical to customer environments.
This data enhances customer trust and plays a pivotal role in mitigating operational risks through informed decision-making.
In conclusion, the choice of radial oil seals is more than a mere selection of components; it's a strategic decision that influences machine reliability, performance, and maintenance costs. For industries ranging from automotive to wind energy, the proper selection and installation of these seals are critical for maintaining operational integrity. As a result, choosing radial oil seals backed by experience, specialized expertise, authoritative recognition, and trustworthiness can significantly contribute to efficient and reliable machinery operation, ultimately providing a competitive edge in an increasingly demanding industrial landscape.