Retainer oil seals have become indispensable components in various mechanical systems, serving as the critical barrier between different environments to prevent lubricant leakage and contamination ingress. These seals play a pivotal role in enhancing an engine or machinery's efficiency and longevity. With decades of evolution and innovation in seal technology, understanding and selecting the right retainer oil seal can dramatically influence a product’s performance.
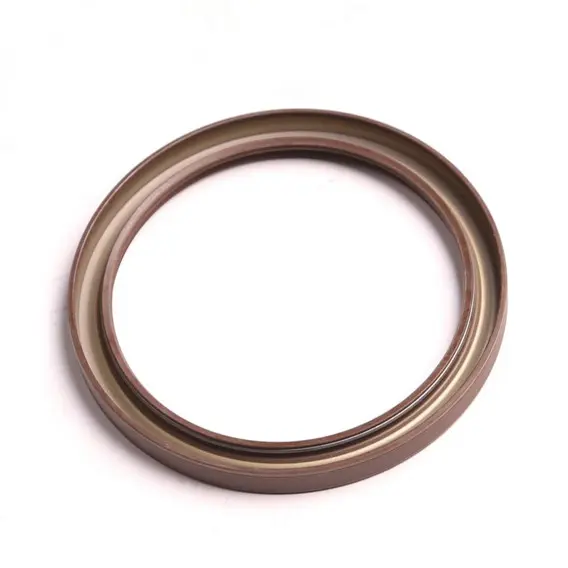
The essence of retainer oil seals lies in their sophisticated design, combining material science and engineering to provide maximum protection. Modern retainer oil seals are crafted using advanced materials such as Viton, Nitrile, and Silicone, each offering unique advantages depending on the application requirements. Viton, for example, is renowned for its exceptional chemical resistance and temperature endurance, making it suitable for high-performance engines and industrial machinery.
Nitrile seals, on the other hand, are favored for their cost-effectiveness and oil resistance, making them ideal for general-use scenarios.
Expertise in the selection and application of retainer oil seals involves analyzing operational conditions, including pressure, temperature, shaft speed, and the type of fluid being retained. A misstep in this critical selection process can lead to premature seal failure, resulting in costly downtime and repairs. It is always recommended to consult with professionals or utilize a reputable manufacturer’s compatibility charts to ensure the selected seal will withstand the demands of the specific application.
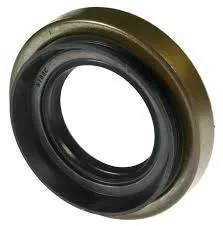
Authoritativeness in the realm of retainer oil seals is often showcased by manufacturers who not only produce seals but also invest in extensive research and development. Leading companies in the industry continuously push the boundaries by enhancing the seal’s design and material composition to meet the rigorous requirements of modern engines and machinery. When selecting a supplier, it is crucial to consider their history of innovation, the testimonials from industry experts, and their adherence to international quality standards such as ISO/TS 16949 and ISO 9001.
retainer oil seal
Trustworthiness in retainer oil seal products is heavily reliant on transparency and reliability in manufacturing processes. Manufacturers who provide clear documentation regarding the product’s technical specifications, alongside offering robust customer support, stand out as trustworthy partners. Ensuring that every batch of seals undergoes rigorous quality testing helps solidify trust and confirms the product's ability to perform under varied operational conditions.
Real-world experiences with retainer oil seals reveal the product's integral role in enhancing system reliability. Users from automotive and industrial sectors consistently report improvements in the lifespan of machinery and reduced maintenance costs due to the effective performance of high-quality retainer oil seals. These testimonials underscore the importance of investing in superior seals rather than opting for cheaper, lower-quality alternatives, which often result in unforeseen costs and operational disruptions.
In conclusion, retainer oil seals are small yet significant components in mechanical systems, offering critical protection that ensures efficient and reliable operation. Selecting the right seal requires a blend of expertise, authoritative sources, and trustworthy manufacturers, all contributing to the product's overall performance. As the industry advances, keeping abreast of innovations and maintaining a robust understanding of application requirements will be key to leveraging the full potential of retainer oil seals.