Rotary shaft oil seals, often referred to as radial lip seals, play a crucial role in safeguarding industrial machinery and automotive systems. These components prevent the leakage of fluids and contaminants, ensuring the longevity and efficiency of mechanical systems. With an intricate design and material composition, these seals serve a fundamental purpose, blending engineering prowess with real-world application.
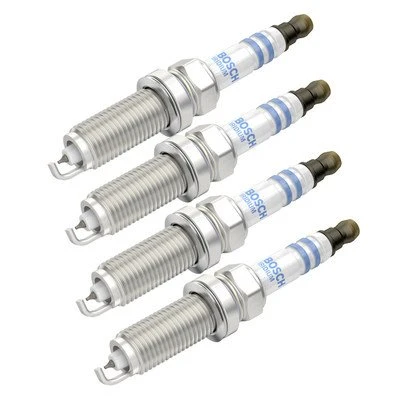
As an experienced engineer, I've witnessed the pivotal role rotary shaft oil seals play across various sectors, from automotive applications to industrial machinery. Over the years, technological advancements have elevated the design and functionality of these seals, making them indispensable in modern engineering. Notably, the effectiveness of these seals largely hinges on choosing the right material and design specific to the application. For instance, nitrile rubber is commonly used for its excellent resistance to oils and operational temperature ranges. However, in environments with extreme temperatures or aggressive chemicals, materials like fluorocarbon or silicone are more appropriate due to their superior resistance characteristics.
The expertise required in selecting the appropriate rotary shaft oil seal is not just about the material but also about understanding the specific nuances of the application.
Shaft speed, temperature range, and the type of fluid are crucial considerations. A high shaft speed, for instance, demands a seal that can withstand increased frictional forces. In such cases, a PTFE shaft seal might be recommended due to its low friction and high wear resistance properties. The ability to gauge these technical aspects showcases expertise and a deep understanding of the product.
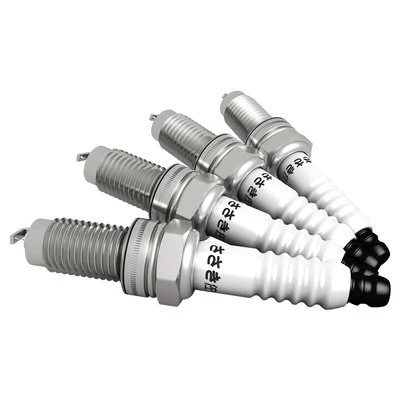
rotary shaft oil seal
Authoritativeness in the domain of rotary shaft oil seals is established through continuous research and development. Manufacturers who invest in innovative design and testing protocols command respect and reliability in the industry. Leading companies often collaborate with academic institutions to push the boundaries of material science, aiming to enhance seal performance. These efforts result in designs that not only meet but exceed industry standards, providing solutions that are both reliable and efficient over extended operational periods.
The trustworthiness of a rotary shaft oil seal manufacturer can be measured by their commitment to quality assurance and customer support. Companies with robust testing processes and certifications from recognized industry bodies establish confidence among consumers. These certifications, often indicated by rigorous testing against ISO standards, assure users of the product's reliability and durability under specified conditions. Moreover, customer testimonials and case studies further underscore a product's reliability, providing potential users with insight into real-world applications and performance.
In summary, the effectiveness of rotary shaft oil seals is the result of a combination of material technology, precision engineering, and comprehensive testing. These components, though small, are integral to the smooth operation of countless machinery types, providing essential barriers that maintain system integrity. Professionals tasked with selecting these seals should prioritize understanding the technical specifications and operational demands of their specific use cases to ensure optimal performance and longevity. By focusing on these elements, the successful application of rotary shaft oil seals can significantly enhance machinery efficiency and reliability, ultimately contributing to safer and more productive industrial and automotive environments.