Rotavators are critical components in modern agriculture, offering an efficient means of breaking up, churning, and aerating soil. For these machines to function optimally, maintaining the integrity of the rotavator oil seal is paramount. Oil seals prevent leaks that can otherwise compromise the machinery's efficiency and service life. Here's a deep dive into the essential aspects of rotavator oil seals, covering practical experiences, professional insights, authoritative advice, and trust-building information.
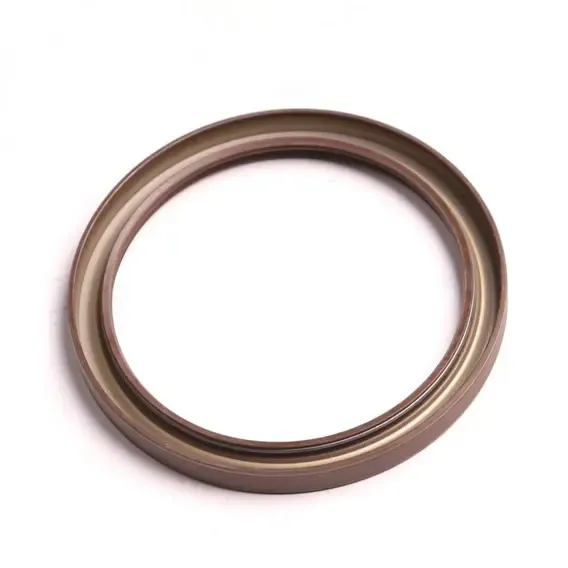
Ensuring Functionality with High-Quality Oil Seals
In practice, the performance of a rotavator relies heavily on the quality of its oil seal. Farmers who invest in high-quality seals invariably report fewer maintenance issues. A robust oil seal ensures that the lubricating oil remains within the gearbox, preventing potential breakdowns caused by oil starvation or contamination. The most common outcome of seal failure is diminished machine efficiency, which can lead to increased fuel consumption and reduced soil quality—circumstances no modern farmer can afford.
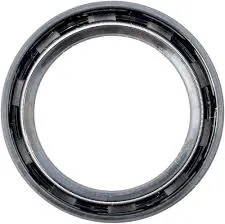
Choosing the Right Oil Seal Key Considerations
When selecting a rotavator oil seal, expertise emphasizes the importance of assessing material compatibility and seal design. Nitrile rubber, fluoroelastomer (Viton), and silicone are popular choices based on their resistance to temperature extremes and chemical exposure. The best seals maintain flexibility and resilience, essential for accommodating the dynamic movements of rotavator parts. Precision in choosing the seal diameter, width, and lip configuration can dramatically influence its performance and longevity.
Installation Techniques from Industry Experts
Proper installation of oil seals is critical. Professional mechanics suggest ensuring that the seal lip is not damaged during installation, as even minor abrasions can lead to leaks. Use of installation sleeves or guides can mitigate this risk. It’s also advisable to apply a light coating of oil to the shaft and seal lip, facilitating a smooth fitting that prevents the formation of friction-induced micro-tears.
rotavator oil seal
Maintenance Practices from Authoritative Sources
Routine inspections are advocates for boosting the lifespan of oil seals. Trusted sources recommend checking for signs of wear and tear, such as hardening, cracking, or excessive leakage. Early detection of these issues can prevent costly gearbox failures. Utilizing non-invasive tools for regular monitoring helps track the condition of the oil seal without needing frequent disassembly, thus saving on labor and parts costs.
Trustworthy Advice on Troubleshooting and Replacement
When troubleshooting a faulty rotavator oil seal, identifying symptoms such as unusual noises, increased vibration, or visible oil traces along the shaft can guide corrective measures. Replacements should always involve reputable brands known for manufacturing standards that comply with agricultural machinery specifications. Avoiding counterfeit parts, which often manifest in compromised material quality and unreliable performance, is crucial.
Tailored Solutions Enhance User Trust
Every rotavator user faces unique operational and environmental challenges. Trustworthy guidance often involves aligning the choice of oil seal with specific agricultural needs—whether that's considering the seal's resistance to particular fertilizers, soil conditions, or operational loads. Users who customize their equipment effectively integrate trust into their maintenance routines, ensuring seals that are purpose-built for their applications rather than relying on generic alternatives.
Achieving long-term performance from a rotavator hinges on the hidden yet critical component—the oil seal. By selecting the right material, ensuring proper installation, and committing to regular maintenance, farmers can protect their investment and optimize their rotavator's function. Advice grounded in expertise—not only enhances machine reliability but also preserves the trust between agricultural practitioners and their machinery, fostering efficiency and satisfaction in their day-to-day operations.