The Indispensable Role of Rubber Tube Gaskets in Industrial Applications
A rubber tube gasket, a seemingly simple yet highly effective component, plays a pivotal role in various industrial applications where sealing and leak prevention are critical. A gasket, fundamentally, is a mechanical seal that fills the space between two or more mating surfaces, preventing leakage from or to the surroundings under compression. When specifically crafted as a rubber tube gasket, it brings forth a unique combination of flexibility, resilience, and durability.
The term rubber denotes a highly elastic polymer material, which, when molded into a tube shape, offers exceptional adaptability and resistance to pressure changes. The tube in rubber tube gaskets refers to their cylindrical form, designed to fit snugly around pipes or tubes, ensuring a secure seal. Gaskets made from rubber are preferred due to their ability to withstand a wide range of temperatures, resist chemicals, and absorb shock, making them ideal for high-pressure and dynamic sealing applications.
There are several types of rubber materials used in manufacturing tube gaskets, each with its own set of properties tailored to specific industrial needs. For instance, Neoprene, known for its resistance to oil and ozone, is often utilized in automotive and chemical processing industries. Silicone rubber, on the other hand, with its excellent heat resistance, finds use in high-temperature environments. Viton, with its superior resistance to harsh chemicals and high temperatures, is a go-to choice for the oil and gas industry Viton, with its superior resistance to harsh chemicals and high temperatures, is a go-to choice for the oil and gas industry
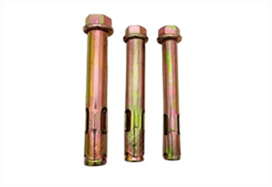
Viton, with its superior resistance to harsh chemicals and high temperatures, is a go-to choice for the oil and gas industry Viton, with its superior resistance to harsh chemicals and high temperatures, is a go-to choice for the oil and gas industry
rubber tube gasket.
The process of creating a rubber tube gasket involves precise molding, cutting, or extrusion techniques to ensure the final product fits perfectly onto the pipe or tube surface. The gasket's design, thickness, and material selection all play crucial roles in determining its performance and longevity. Engineers often rely on computer-aided design (CAD) software to create intricate gasket profiles that can handle complex geometries and ensure optimal sealing.
Once installed, rubber tube gaskets provide a reliable barrier against fluid leaks, maintaining system integrity and preventing potential safety hazards. Regular inspection and timely replacement are necessary to maintain their effectiveness, as over time, gaskets can degrade due to exposure to environmental factors or continuous pressure.
In conclusion, the rubber tube gasket, though often overlooked, is a vital element in numerous industrial processes. Its versatility, durability, and sealing capabilities make it an indispensable component in piping systems across various sectors, from automotive and chemical engineering to food and beverage processing. Understanding the importance of these gaskets and selecting the right material for each application can significantly contribute to overall system efficiency and safety.