In the dynamic world of industrial components, few items are as foundational yet as critical as the rubber gasket. These seemingly simple products play a crucial role in ensuring the efficiency and safety of countless mechanisms, from household appliances to complex industrial equipment. Understanding their function and applications requires not only a basic awareness of their use but a deep dive into the nuances that define their quality, application, and importance.
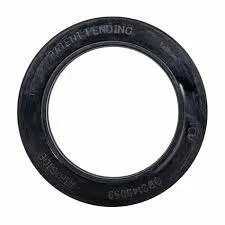
Rubber gaskets are essential sealing components designed to prevent leaks between two surfaces. Their primary function is to create a static seal, ensuring that fluids, gases, or other substances do not escape from or penetrate into systems where they shouldn't be. The expertise in crafting and applying these gaskets, therefore, becomes paramount in industrial design. For instance, in the automotive industry, the precision of rubber gaskets can mean the difference between a vehicle that runs smoothly and one that is plagued by leaks and inefficiencies.
From a professional perspective, the rubber material used in gaskets is chosen based on its compatibility with the substances it will be sealing against, as well as the environmental conditions it will be exposed to. Neoprene, EPDM, and silicone are popular rubber choices due to their robust resistance to factors such as heat, oil, and weather, but each has its unique properties. For example, neoprene is favored for its excellent chemical stability and oil resistance, making it ideal for automotive applications, while EPDM is celebrated for its superior resistance to heat, ozone, and weather, making it suitable for outdoor applications.
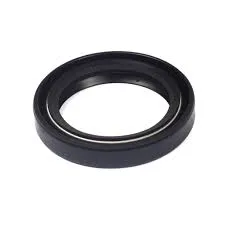
In terms of production, the accuracy of gaskets is achieved through meticulously crafted molds and precision cutting techniques. Expertise in their manufacturing ensures each gasket maintains tight tolerances, crucial for their role as effective seals. Manufacturing techniques have evolved with advancements in technology, and today, custom gaskets can be fabricated using CNC machinery and water jet cutting, allowing for the utmost precision and reduction of waste materials.
The authority on choosing the right rubber gasket comes from understanding the specific requirements of your application. Engineers and designers must consider the pressure levels the gasket will face, the temperatures it will endure, and the chemical compatibility required. This deep understanding is where professional consultation becomes invaluable, ensuring the gaskets selected will provide long-lasting and reliable performance.
rubber gasket
When it comes to trustworthiness, the sourcing and testing of rubber gaskets are pivotal. High-quality gaskets undergo stringent testing to meet industry standards, ensuring they can withstand the stated pressures and temperatures without degrading. Trust in a rubber gasket brand or manufacturer is built through their adherence to ISO and other relevant certifications, demonstrating their commitment to quality and reliability.
End users often overlook these complex considerations, yet the real-world experience with rubber gaskets showcases their undeniable importance. Experienced industry professionals can attest to scenarios where inferior gaskets led to catastrophic equipment failures, underscoring the critical role of using well-crafted, high-quality components. This emphasizes the importance of choosing gaskets not just on price, but on validated performance data, manufacturer reputation, and after-sales support.
Overall, rubber gaskets might seem like a small component, but their impact on the performance and safety of systems cannot be overstated. By incorporating decades of professional expertise and leveraging advances in material science and manufacturing technology, businesses can ensure that they select the most effective gaskets for their needs. This strategic approach safeguards equipment functionality and longevity, ultimately driving operational excellence and reducing downtime.
In summary, the choice and application of rubber gaskets is a testament to the balance between material science, engineering expertise, and stringent quality assurance. For industries reliant on these components, investing in the right knowledge and resources to select and maintain high-quality rubber gaskets can significantly influence their operational success and longevity.