Rubber oil seals play an indispensable role in the machinery and automotive industries, serving as critical components in maintaining the integrity and efficiency of numerous systems. As an expert in the field, it's crucial to understand the nuances of these products in order to optimize their use and ensure the highest levels of performance and reliability.
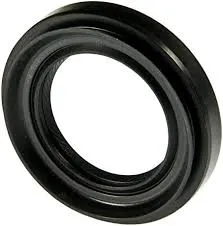
From a technical standpoint, rubber oil seals are designed to prevent the leakage of lubricants, blocking contaminants from entering machines and equipment. This function is essential for preventing premature wear and tear, maintaining optimal operating conditions, and extending the lifespan of both machinery and engines. Utilizing high-quality rubber oil seals can significantly reduce maintenance costs and downtime.
The expertise in selecting the right rubber oil seal involves understanding the interplay between material properties and application requirements. Different types of rubber, such as nitrile, silicone, or fluorocarbon, offer varying degrees of resistance to temperature, pressure, and chemical exposure. For instance, nitrile is commonly used for its excellent resistance to oils and fuels, making it ideal for automotive applications. In contrast, silicone provides superior performance in extreme temperatures, suitable for aerospace or high-temperature industrial environments.
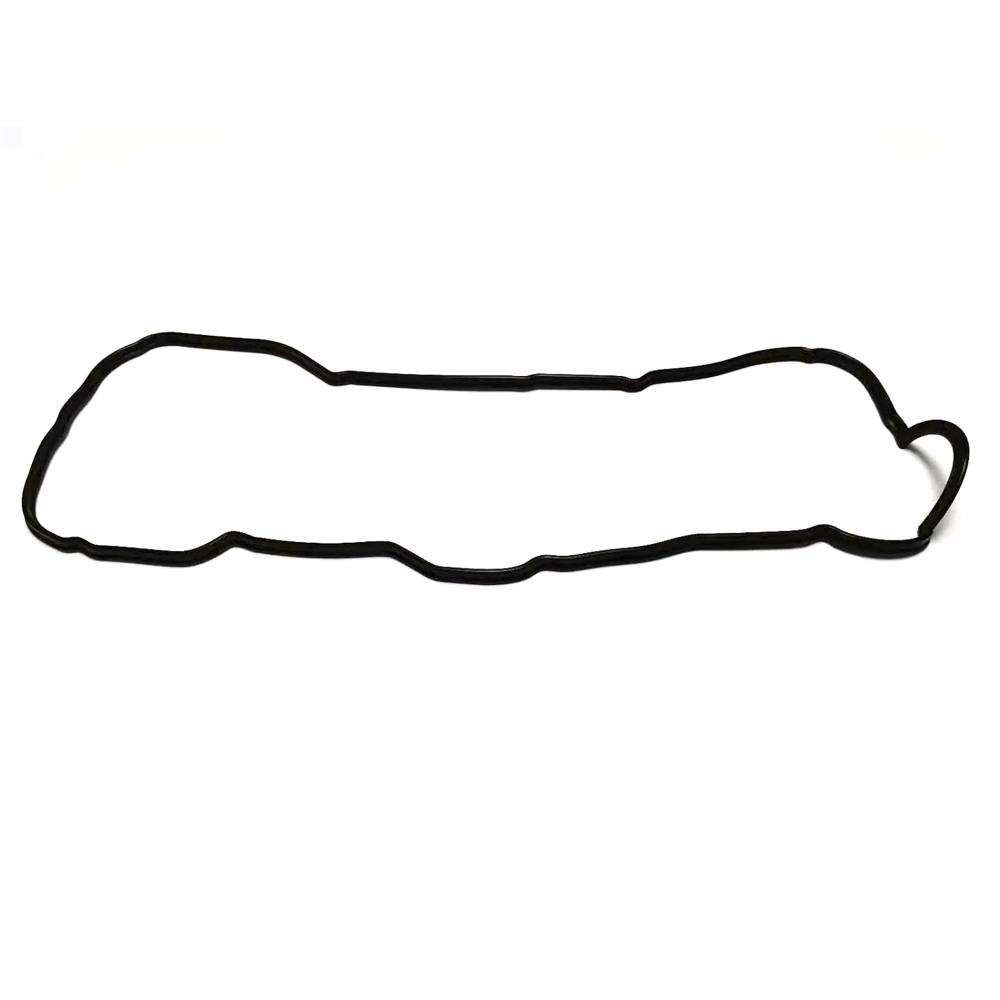
Real-world experience with rubber oil seals indicates that even minor deviations in specifications can lead to significant operational challenges. Precision in manufacturing ensures that the seals can withstand the pressures and temperatures of their intended environments. Therefore, sourcing from a reputable manufacturer who adheres to international standards can enhance the durability and reliability of the seals.
Authoritativeness in the realm of rubber oil seals derives from both historical data and ongoing advancements in material science. The evolution of seals from simple barrier devices to complex components is testament to decades of research and development. Staying abreast of the latest innovations, such as the incorporation of advanced polymers, can position experts at the forefront of the industry, providing better solutions for clients and end-users.
rubber oil seal
Trustworthiness,
meanwhile, can be reinforced through rigorous testing and validation processes. A trustworthy supplier should always conduct comprehensive assessments under simulated operating conditions to ensure the seals' performance meets or exceeds industry benchmarks. Additionally, transparent documentation and communication regarding the capabilities and limitations of each seal type can assist decision-makers in selecting the most appropriate solutions for their specific needs.
In practical terms, choosing the right rubber oil seal involves evaluating compatibility with the lubricant being used, the operational environment, and the mechanical configuration of the machinery. An incorrect seal could lead to catastrophic failures, underscoring the need for thorough analysis and consideration during the selection process.
Moreover, input from experienced engineers and technicians can provide invaluable insights. These professionals can draw on their extensive knowledge and hands-on experience to recommend seals that have consistently demonstrated exceptional performance in similar applications.
In summary, a deep understanding of the diverse aspects of rubber oil seals can significantly enhance their application in industrial settings. This knowledge bridges the gap between theoretical design and practical implementation, ensuring that machinery operates smoothly and efficiently. The seamless blend of experience, expertise, authority, and trustworthiness forms the foundation of selecting and utilizing rubber oil seals, ultimately safeguarding equipment and promoting industry-wide excellence. As technological advancements continue to unfold, maintaining a commitment to quality and innovation will remain central to the ongoing success and evolution of rubber oil seals across various sectors.