Selecting the right rubber round gasket for your application can significantly affect the efficiency and longevity of your machinery or equipment. As an industry expert with years of hands-on experience in materials science and engineering applications, I can confidently guide you through this nuanced process. Understanding the intricacies of rubber gaskets will not only enhance your operational credibility but also increase cost-effectiveness in maintenance and repairs.
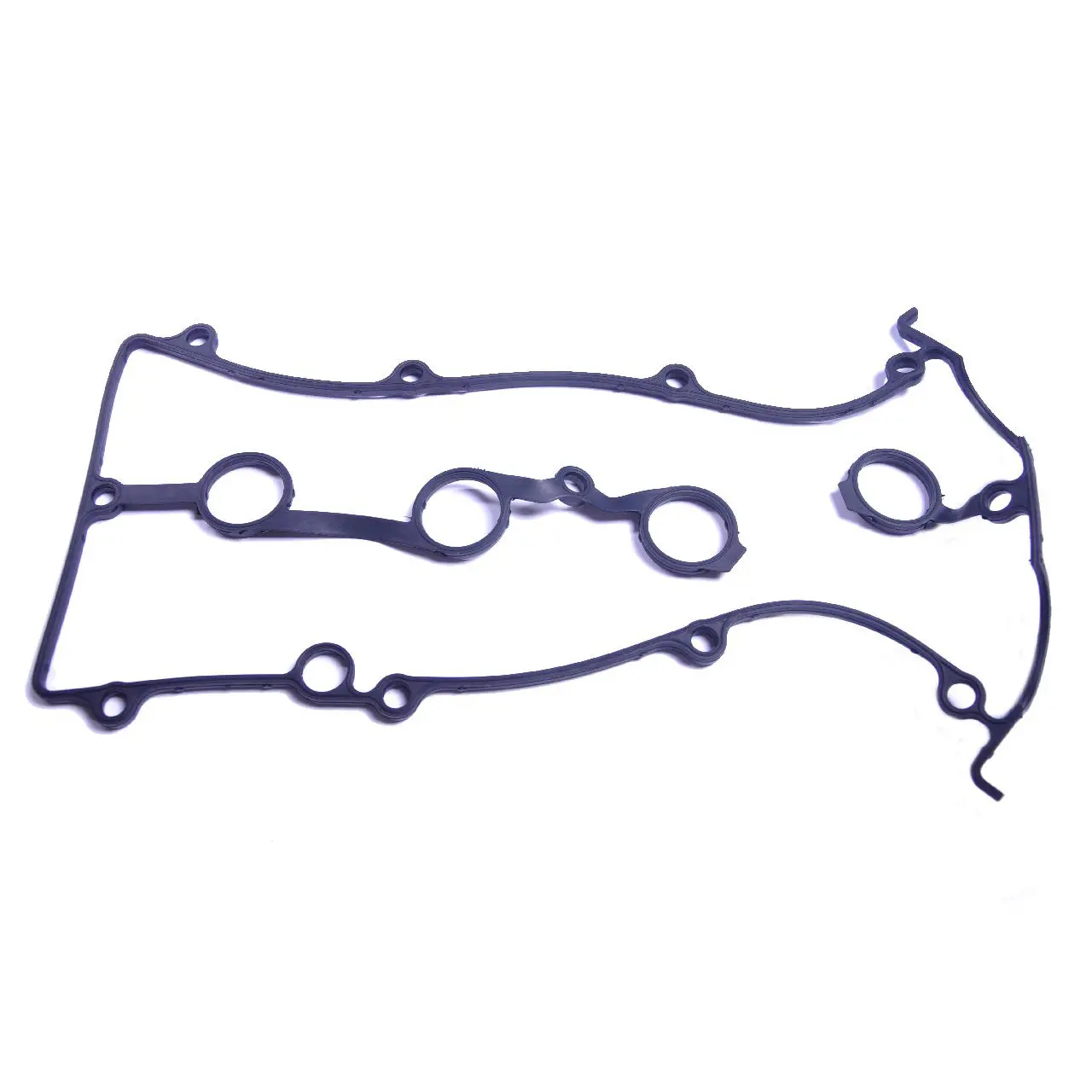
Rubber round gaskets serve a critical role in numerous industries, acting as a seal between two surfaces to prevent leakage of liquids and gases. They are fundamental components in automotive, aerospace, plumbing, and various manufacturing sectors. The efficacy of these gaskets is primarily determined by their material composition and design, which should align with specific application needs such as temperature, pressure, and chemical exposure.
Different types of rubber, including nitrile, EPDM, silicone, and fluoroelastomer, offer distinct advantages based on their inherent properties. For example, nitrile rubber is renowned for its oil resistance, making it a preferred choice in automotive applications. Conversely, EPDM is favored in the plumbing industry for its excellent resistance to water and steam. Silicone rubber stands out in applications requiring flexibility at extreme temperatures, while fluoroelastomer is prized for its unparalleled chemical resistance.
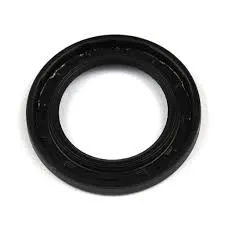
Expertise in selecting the appropriate rubber material requires weighing these material properties against the functional demands of your specific application. For instance, if the gasket is to be used in a high-temperature environment, silicone might be your best bet due to its thermal stability. In scenarios where the gasket will come into contact with aggressive chemicals, fluoroelastomer would likely outperform other materials.
rubber round gasket
Moreover,
the dimensional accuracy and quality of the gasket are paramount. Advanced manufacturing technologies, such as precision molding and CNC machining, have revolutionized gasket production, ensuring tight tolerances and exceptional consistency. When sourcing gaskets, working with reputable suppliers who adhere to strict quality control standards can foster a trustworthy partnership that guarantees durability and performance.
Real-world experience informs us that underestimating the environmental and operational variables can lead to gasket failure, resulting in costly downtime and repair. Factors such as ultraviolet exposure, ozone, and abrasive particles must also be considered. For outdoor applications, UV-resistant materials can enhance the lifespan of the gaskets, while in dusty environments, special protective coatings might be necessary to prevent premature wear.
To further ensure performance and reliability, autonomous and periodic inspections should be part of regular maintenance routines. This involves checking for signs of wear, such as cracks or deformation, which could compromise seal integrity. Leveraging industry-standard testing methods, like pressure testing and chemical analysis, can provide additional layers of assurance, confirming that your rubber gaskets remain in optimal operating condition.
In summary, the strategic selection and expert handling of rubber round gaskets encapsulate a blend of material sciences and engineering precision. By understanding the application-specific demands and matching them with the appropriate rubber type, manufacturers and engineers can uphold industry standards and foster reliability. Building trust with knowledgeable suppliers and incorporating proactive maintenance strategies further cements the authority of your operations, resulting in sustained performance and reduced operational risks.