Sheet gaskets serve as critical components in a wide range of industries due to their excellent sealing capabilities. These gaskets, often crafted from materials such as rubber, graphite, or PTFE, provide a reliable barrier against leaks, facilitating smooth operations and ensuring safety across various applications. The significance of sheet gaskets in industrial scenarios cannot be overstated, given their role in preventing costly downtime and maintaining integrity in piping and equipment systems.

Having worked with numerous brands and types of sheet gaskets over the years, my experience points to the importance of selecting the right material and thickness for the intended application. Industries from petrochemical to food processing rely heavily on the effectiveness of these gaskets, not just to prevent leaks, but to ensure compliance with environmental and safety regulations. The choice of a sheet gasket could impact not only the maintenance schedules but also the overall operational costs.
On expertise, understanding the compatibility of gasket materials with various chemicals and temperatures is essential. For example, PTFE sheet gaskets are prized for their chemical resistance and ability to withstand high temperatures, making them ideal for aggressive media. Meanwhile,
rubber gaskets excel in applications requiring flexibility and resilience. The technical specifications such as tensile strength, compression set, and hardness should guide the selection process to ensure longevity and effectiveness of the seal.
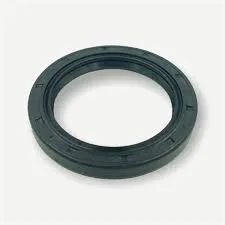
Authoritativeness in the field of sheet gaskets is showcased by the rigorous testing and certifications these products undergo. Industry standards, such as those set by ASTM and ISO, establish the baseline for performance and reliability expectations. Engineers and procurement specialists should seek gaskets that meet these standards to ensure they are using components that are both tested and trusted. Manufacturers that achieve these certifications often have a higher level of scrutiny, ensuring that their products deliver under the most demanding circumstances.
sheet gaskets
Building trustworthiness, particularly in a product as crucial as a gasket, involves transparency in material sourcing and manufacturing processes. Responsible manufacturers provide detailed datasheets and testing results, allowing users to verify the performance claims. Furthermore, involvement in industry associations and staying abreast of technological advancements also enhances credibility. For instance, innovations like expanded graphite gaskets offer advancements in thermal conductivity and sealing efficiency, which were developed to address specific challenges faced by end-users.
In practice, the use of gaskets extends beyond the scope of functionality; they are integral to system designing and operational efficiencies. Regular inspection and replacement protocols must be instituted as part of preventive maintenance strategies. Understanding the lifecycle of a sheet gasket and its behavior in specific applications ensures operational integrity.
Case studies and field data provide invaluable insights into the real-world application of sheet gaskets. Anecdotal evidence from a chemical plant that reduced its leak incidents by 40% after switching to a high-performance PTFE gasket underscores the impact of material choice on operational efficiency. Such examples highlight the importance of coupling technical know-how with practical experience to meet industry demands effectively.
In conclusion, sheet gaskets are indispensable in maintaining system reliability across various industries. Selecting the appropriate gasket involves a nuanced understanding of material science, industry standards, and application requirements. By considering these aspects, companies can ensure safety, reduce downtime, and achieve compliance with regulatory standards, ultimately fostering a seamless operational environment.