The Unfading Significance of Silicone Oil Seals in Modern Industry
Silicone oil seals, an integral part of various engineering and manufacturing processes, have carved a niche for themselves due to their exceptional properties and versatility. These seals, composed primarily of silicone rubber combined with silicone oil, are designed to prevent the leakage of fluids or gases, while also protecting components from environmental contaminants. They play a pivotal role in ensuring the efficient and safe operation of machinery across a wide spectrum of industries.
The key advantage of silicone oil seals lies in their resilience and durability. Silicone, as a material, is known for its ability to maintain flexibility over a broad temperature range, from -100°C to 200°C. This makes it ideal for applications where extreme temperatures are common, such as in automotive, aerospace, and chemical processing industries. The oil component further enhances the seal's lubricating properties, reducing friction and wear on mating surfaces.
Moreover, silicone oil seals exhibit excellent resistance to ozone, weathering, and aging, which significantly extends their service life. They are also resistant to a variety of chemicals, making them suitable for use in harsh chemical environments. In the medical and food industries, where hygiene is paramount, silicone oil seals are preferred due to their non-toxicity and ease of cleaning.
The versatility of silicone oil seals is another compelling factor
The versatility of silicone oil seals is another compelling factor
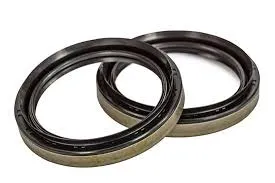
The versatility of silicone oil seals is another compelling factor
The versatility of silicone oil seals is another compelling factor
silicone oil seal. They can be tailored to meet specific requirements, whether it's customizing the hardness, shape, or size to fit unique applications. They can be used in static or dynamic sealing situations, sealing everything from hydraulic fluids to aggressive solvents.
Despite these benefits, proper installation and maintenance are crucial for optimal performance. Incorrect installation can lead to seal failure, potentially causing equipment downtime and costly repairs. Regular inspection and timely replacement of worn seals are essential practices to ensure continued reliability.
In conclusion, silicone oil seals have become indispensable in modern industry, providing reliable sealing solutions in demanding conditions. Their robustness, adaptability, and chemical resistance make them a go-to choice for engineers worldwide. As technology continues to advance, we can expect further innovations in silicone oil seal design and application, solidifying their position in the realm of sealing technology. Whether it's safeguarding critical machinery in extreme conditions or ensuring in pharmaceuticals, silicone oil seals continue to play a silent but vital role.