In the intricate world of machinery, small oil seals play a crucial role that is often underestimated. These components, though diminutive in size, serve as the guardians of various mechanical systems, keeping them functional and efficient. Their importance extends across industries—from automotive to aerospace—making them indispensable in maintaining the integrity and performance of countless applications.
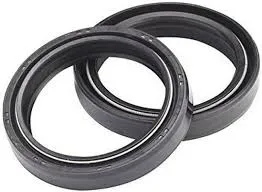
Understanding the function of small oil seals is pivotal for anyone delving into mechanical maintenance and design. These seals are typically constructed from high-quality elastomers, which provide the flexibility needed to create a snug fit against moving parts. The primary purpose of these seals is to retain lubricants while preventing contaminants like dirt, dust, and moisture from entering the machinery. This dual-functionality not only ensures the smooth operation of mechanical components but also significantly extends their lifespan by preventing premature wear and tear.
Professionals in the field of engineering and design know that the selection of the right oil seal is critical. Factors such as temperature, pressure, lubrication type, and the environment in which the seal will operate must be considered to ensure optimal performance. For instance, in high-temperature environments, seals made from materials such as fluoroelastomers may be necessary to withstand the heat. Similarly, in challenging chemical environments, seals composed of polytetrafluoroethylene (PTFE) are often favored due to their exceptional chemical resistance.

From a technical perspective, the structure of small oil seals involves components like the sealing lip, the metallic insert, and the garter spring. The sealing lip is designed to maintain constant pressure on the shaft, which is essential in preventing leaks. The garter spring enhances the seal’s effectiveness by ensuring that the lip maintains the necessary pressure over the shaft even as it undergoes dynamic movement. This synergy of components underscores the engineering precision embodied in the design of oil seals.
small oil seals
Authority in the oil seals niche can further be established by acknowledging the innovations and advancements in seal technology. Recent developments have introduced self-lubricating seals and seals embedded with sensors to monitor conditions such as pressure and temperature in real time. These advancements highlight how oil seals are becoming not just passive components but active elements of machinery monitoring and maintenance, enhancing their value proposition in modern engineering.
Trusted professionals in the field will always emphasize the importance of proper installation and maintenance of oil seals to ensure their longevity and effectiveness. Regular inspections for signs of wear, such as hardening, cracking, or splitting, can preempt failures. Furthermore,
understanding the load and speed capabilities of different seals is crucial. Misapplication can lead to compromised machinery performance and costly downtime, which reinforces the value of expertise in selecting and managing these vital components.
In conclusion, small oil seals may appear to be minor components in the grand scope of mechanics, but their role is profoundly significant. By retaining crucial lubricants and excluding harmful contaminants, they protect the core functionalities of machines. For engineers and designers, appreciating the complexity and necessary precision in selecting the right oil seal translates into enhanced reliability and performance of systems. As technology progresses, so does the innovation in oil seal design, continuing to safeguard our machinery and advance the mechanical world with reliability and trust.