Thick rubber gaskets play a crucial role in a wide array of industries, from automotive and aerospace to household appliances and industrial equipment. As a seasoned expert in the field of rubber engineering and manufacturing, I have explored the multifaceted applications and unparalleled advantages these gaskets offer, cementing them as an indispensable component in numerous sectors.
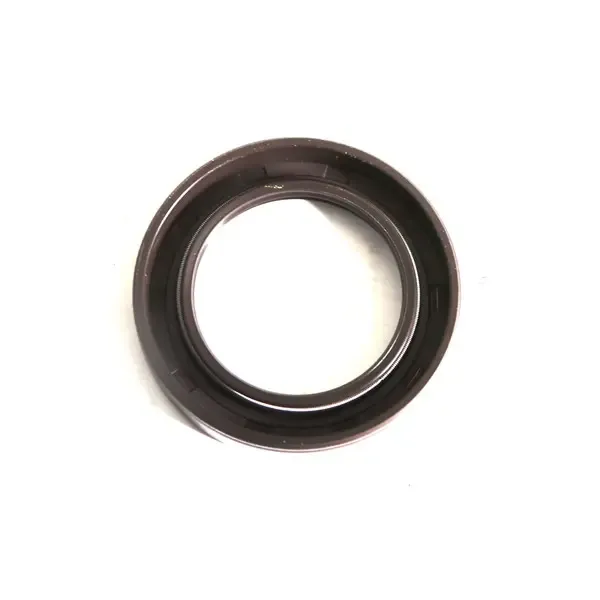
The thickness of a rubber gasket significantly enhances its ability to seal, providing a robust barrier against the escape or entry of gases and liquids. This property is particularly useful in high-pressure environments such as engine assemblies and hydraulic systems, where even the slightest leakage could lead to costly malfunctions or safety hazards. The precision in manufacturing thick rubber gaskets ensures that they can withstand extreme environmental conditions, safeguarded against adverse temperatures and potentially harmful chemical exposures.
A deep understanding of material science is pivotal in crafting the perfect rubber gasket. The choice of elastomer can dramatically affect performance. For instance, nitrile rubber is often chosen for applications involving oils and fuels due to its remarkable resistance to these substances. Conversely, silicone rubber might be preferred in the food and pharmaceutical industries thanks to its compliance with health regulations and its ability to endure a broad range of temperatures. EPDM rubber finds its use extensively in weather-resistant applications, thanks to its excellent resistance to heat, ozone, and weathering.
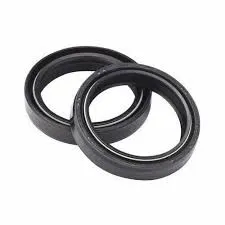
The expertise in designing thick rubber gaskets extends beyond merely picking the right material. It involves a keen understanding of the gasket's application environment. Thickness optimization is a crucial factor; too thick, and the gasket may not fit properly in tight spaces or may impede mechanical efficiency. Too thin, and it might fail under pressure or temperature fluctuations. Engineers use sophisticated modeling tools to simulate the conditions a gasket will face, refining its specifications until it achieves the perfect balance between durability and flexibility.
Trust in thick rubber gaskets is built on rigorous testing and quality control. Before reaching the market, these gaskets undergo a battery of standardized tests that examine their resilience under pressure, tensile strength, compression set, and aging. These tests are vital in ensuring the gaskets perform reliably over time and under the specific conditions they are designed for. Reputation matters in industries dependent on these components, and manufacturers with established histories of delivering high-quality rubber gaskets are often preferred partners.
thick rubber gasket
Authoritative voices in the industry advocate continuous development in gasket technology, embracing advances in materials science and manufacturing processes. By integrating new technologies such as 3D printing and advanced composite materials, manufacturers can optimize gasket designs for unprecedented levels of efficiency and reliability. These innovations promise to push the boundaries of what thick rubber gaskets can achieve, ensuring they meet the ever-evolving demands of global industries.
Real-world experience attests to the transformative power of thick rubber gaskets in machinery performance and longevity. When applied expertly, these gaskets contribute to the reduction of maintenance costs and downtime. For example, a properly fitted gasket in an HVAC system can significantly enhance energy efficiency by ensuring airtight seals. Similarly, in automotive applications, durable gaskets help maintain engine integrity, prolonging vehicle lifespan and reducing fuel consumption due to minimized emissions leakage.
A testament to their importance, thick rubber gaskets are continually scrutinized by regulatory bodies to ensure compliance with stringent environmental and safety standards. Companies committed to corporate responsibility prioritize using environmentally-friendly materials, and in turn, these gaskets align with sustainable practices. This commitment to eco-friendly solutions is increasingly relevant in today's world, as consumers become more informed and conscientious about sustainability.
In conclusion, thick rubber gaskets are a testament to the synergy between advanced engineering, material science, and industry expertise. Their utility across different fields is unmatched, driven by their ability to adapt and perform under various conditions. As industries continue to evolve, the optimization and innovation in rubber gasket technology promise to uphold their pivotal role, ensuring reliable performance, enhancing operational efficiency, and contributing to a more sustainable future.