In the rapidly advancing world of industrial applications, rubber gaskets stand out as crucial components ensuring the integrity and performance of machinery and equipment. While many types of gaskets are available, rubber gaskets uniquely combine flexibility, resilience, and adaptability, qualities that make them indispensable across various industries.
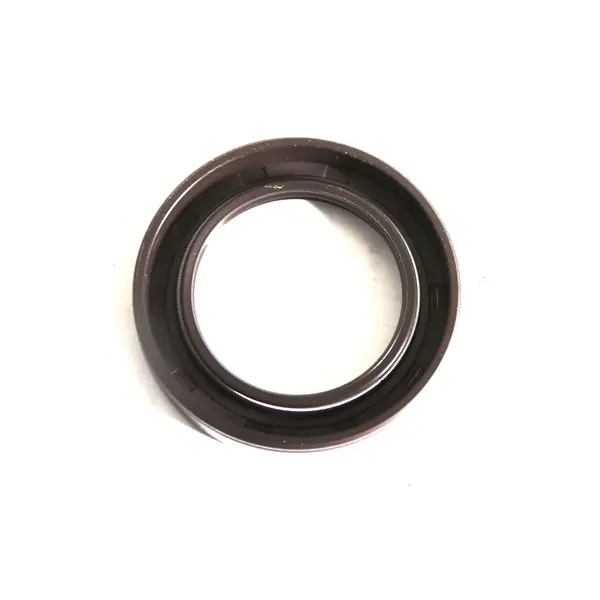
Rubber gaskets function primarily as seals, preventing leaks between different surfaces while enduring varying pressures and temperatures. Made from materials such as silicone, EPDM, neoprene, and nitrile, these gaskets are engineered to meet specific needs, reflecting their versatility and suitability for diverse applications.
Experience Real-world Benefits

In a manufacturing setup, the significance of a robust sealing solution cannot be understated. Take, for example, a beverage production company that relies on large-scale machinery to bottle drinks. Here, rubber gaskets are pivotal in maintaining the sanitary conditions required for food-grade applications. These seals ensure that no contaminants infiltrate the process, safeguarding product quality and consumer health.
Moreover,
automotive industries benefit significantly from rubber gaskets. They are commonly used in engines to seal components, such as cylinder head gaskets, valve covers, and intake manifolds, effectively preventing the leakage of oil and coolant. This enhances engine efficiency and longevity while reducing maintenance costs.
Expertise Understanding Material Selection
The expertise involved in selecting the right type of rubber gasket is critical. Knowledge of the operating environment, including exposure to chemicals, heat, and pressure, informs the appropriate material choice. For example, silicone gaskets are favored for high-temperature applications due to their excellent thermal stability, whereas EPDM gaskets are ideal for exterior applications given their outstanding resistance to weathering and UV exposure.
Professionals must also consider the physical properties required, such as durometer hardness, to ensure that the gasket provides the correct amount of compression and rebound. Precision in choosing the right material results in enhanced performance and increased lifespan of the gasket within the application.
u rubber gasket
Authoritativeness Industry Standards and Compliance
Manufacturers of rubber gaskets must adhere to stringent industry standards to provide products that customers can trust. Compliance with standards such as ASTM D2000, which provides a classification system for rubber products, ensures that the gaskets meet rigorous specifications for physical and chemical properties. This not only verifies the quality of the gaskets but also assures users of their reliability for intended applications.
In industries such as pharmaceuticals or food processing, gaskets must also comply with FDA regulations, highlighting the importance of using materials that are safe for human contact. This level of compliance underscores the manufacturer's commitment to delivering trustworthy and high-quality solutions.
Trustworthiness Building Confidence through Proven Solutions
The trustworthiness of rubber gaskets rests on the legacy of their performance and the satisfaction of their users. Customer testimonials and case studies often reveal the success stories behind these products. A construction company might extol the virtues of neoprene gaskets for their resilience against harsh environmental conditions, bridging the gap between traditional construction methodologies and modern performance demands.
Furthermore, a history of innovation in rubber gasket design and manufacturing can bolster trust. When a manufacturer continually invests in research and development to enhance gasket properties, such as improving their resistance to extreme temperature fluctuations or increasing their chemical inertness, it reassures customers of their long-term commitment to quality and advancement.
In conclusion, the profound impact of rubber gaskets on industrial applications cannot be overstated. Their versatility, backed by deep industry expertise, adherence to authoritative standards, and proven reliability, makes them a trusted choice across various sectors. When engineered and utilized correctly, rubber gaskets not only fulfill their intended sealant roles but also contribute significantly to operational efficiency, safety, and longevity, underscoring their indispensable role in today's technological landscape.