In the intricate world of industrial applications, die cut silicone gaskets hold a pivotal role, yet their significance often goes unnoticed to those unfamiliar with their widespread applications. These indispensable components, crafted from high-quality silicone, are tailored to meet specific sealing requirements across various industries. Their versatility and durability make them highly sought after, contributing to the efficiency and reliability of countless machines and devices.
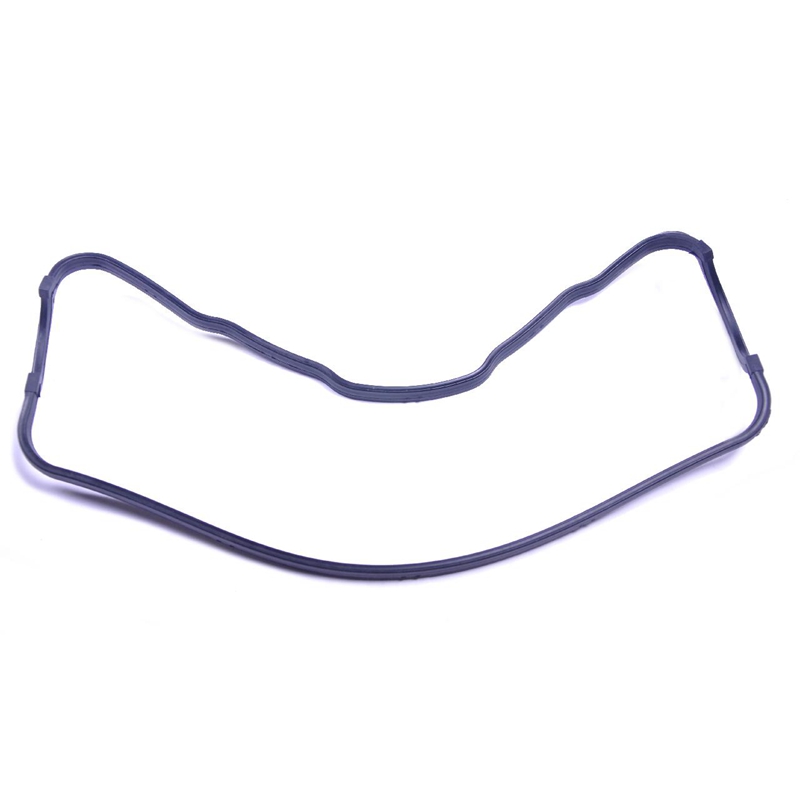
Die cut silicone gaskets are engineered with precision, specifically using the die-cutting process, which allows for custom shapes and designs. This method involves using a specialized machine equipped with sharp steel blades, cutting the silicone material into exact dimensions as required by the application. The result is a gasket that not only fits perfectly but also performs optimally under diverse conditions.
The choice of silicone as a material for these gaskets is crucial, primarily due to its exceptional properties. Silicone gaskets are renowned for their remarkable thermal stability, often functioning efficiently in temperatures ranging from as low as -60°C to as high as 230°C. This broad temperature range makes them ideal for both high-heat environments, such as automotive engines, and cold conditions, including refrigeration systems. Additionally, silicone exhibits excellent weathering properties, resilience against UV light, ozone, and other environmental factors, ensuring longevity even when exposed to challenging outdoor conditions.

In terms of experience, many industries have shifted to silicone gaskets for their unique flexibility and adaptability. For instance, the automotive industry leverages these gaskets for everything from sealing engine components to preventing leaks in the intricate HVAC systems of modern vehicles. Their ability to withstand harsh environments and repeated mechanical stress without losing effectiveness makes them invaluable. Moreover, in the medical sector, silicone gaskets are indispensable for the manufacture of respiratory devices and surgical instruments, where sterility and resilience against chemical exposure are critical.
die cut silicone gaskets
With expertise in materials engineering, manufacturers of die cut silicone gaskets bring a wealth of knowledge and technical skill to the table. They understand the importance of precision in applications where even the smallest discrepancies can lead to significant performance issues. The collaboration between material scientists and engineers ensures that the gaskets meet stringent industry standards while remaining cost-effective. This synergy is essential in applications such as aerospace, where the reliability and safety of every component are paramount.
From an authoritative standpoint, die cut silicone gaskets have become the subject of various studies, highlighting their effectiveness across multiple domains. Research has demonstrated their superior performance compared to traditional materials like rubber or cork, particularly in applications requiring high flexibility under fluctuating pressures. This has led to a wide acceptance of silicone gaskets as a standard sealing solution in both emerging and established fields, further solidifying their authority within the sealing industry.
Trustworthiness is embedded in the production of silicone gaskets, where quality control is a paramount concern. Leading manufacturers adhere to international standards, such as ISO and ASTM, to ensure each gasket meets the necessary performance specifications. Rigorous testing procedures, including compression and tensile strength tests, guarantee that the gaskets can withstand not only environmental challenges but also meet customer-specific operational demands. This commitment to quality and reliability has built a foundation of trust among industries that depend on these components to safeguard their systems.
In conclusion, die cut silicone gaskets are more than just sealing solutions— they are vital components that enhance the performance and safety of a wide range of machinery and equipment. Their ability to adapt to various conditions, coupled with the expertise and stringent standards upheld by manufacturers, make them a cornerstone in industrial applications. Through continuous innovation and adherence to high-quality standards, these gaskets not only meet but exceed the expectations placed upon them, standing as a testament to their critical role in modern industrial engineering.