Oil seals, often masquerading subtly within machinery, are critical components that ensure the operational efficiency and longevity of many devices and vehicles. Understanding the different types of oil seals, their applications, and characteristics can significantly impact the maintenance routines, operational efficiency, and trustworthiness of industrial and automotive operations.
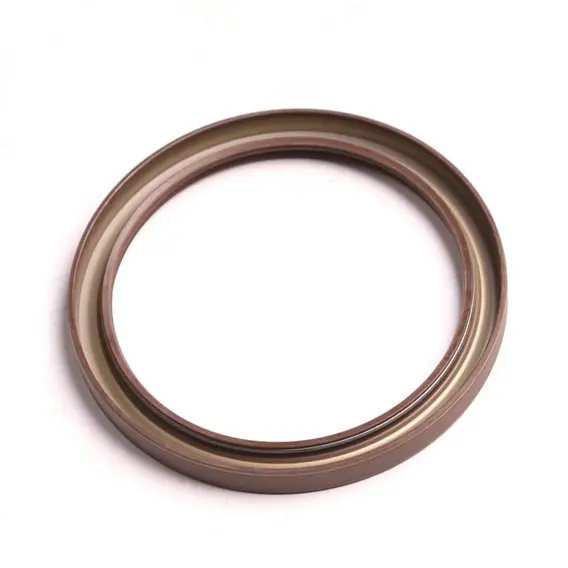
Oil seals, also known as radial lip seals or rotary shaft seals, are fundamental in preventing lubricant leakage and keeping contaminants out, thereby protecting the integrity of the machinery. These seals come in various types, each catering to specific needs and environments.
1. Rubber Oil Seals Among the most common, rubber oil seals are prized for their elasticity and waterproof qualities. These seals are typically made from nitrile rubber or fluorocarbon, providing excellent resistance to oil, chemical degradation, and temperature fluctuations. Their application is prevalent in automotive industries, where they prevent oil leakage in engines and gearboxes, ensuring efficient performance under variable conditions. The material composition makes them suitable for temperatures ranging between -40°C to +120°C, broad enough for most industrial applications.
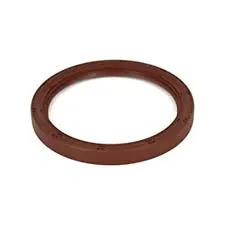
2. Metal-Cased Oil Seals Constructed from a combination of metal and rubber, these seals offer heightened durability and rigidity. The metal case provides structural integrity, while the rubber lip maintains a tight seal against the shaft. These are extensively used in heavy machinery and environments where pressure and speed are elevated, such as in hydraulic systems and industrial pumps. Their robust design extends their lifespan, even in environments with high friction and heat.
3. Fabric Reinforced Oil Seals When dealing with extreme pressure environments, fabric-reinforced oil seals are a reliable choice. The fabric layers enhance the seal's structural strength and pressure resistance, making them ideal for high-stress environments such as aviation and marine applications. Their ability to maintain integrity under pressure is crucial for safety and operational efficiency in critical industry sectors.
different types of oil seals
4. PTFE Oil Seals Polytetrafluoroethylene (PTFE) oil seals serve industries where chemical exposure and high temperatures are routine. PTFE's non-reactive nature makes these seals highly resistant to aggressive chemicals and extreme temperatures, ranging from -200°C to +250°C. They are indispensable in chemical processing industries and environments where other materials might degrade rapidly.
5. Labyrinth Seals Unlike conventional oil seals, labyrinth seals don't contact the rotating shaft. Instead, they use a complex maze-like design to minimize the passage of contaminants and fluids. These are optimal for high-speed applications and situations where minimal friction is necessary, such as in turbo machinery. Labyrinth seals are particularly valued for their longevity and ability to handle thermal expansion and contraction without compromising the seal.
A crucial aspect of selecting the appropriate oil seal lies in understanding the specific environmental challenges the machinery will face. From harsh chemicals and extreme temperatures to high-pressure conditions, the right oil seal not only ensures operational efficiency but also protects against costly downtime and repairs.
Proper installation and regular maintenance of oil seals are essential. Even the best oil seals can fail if improperly installed or without regular checks for wear and tear. This includes ensuring the shafts are smooth and without defects, as rough surfaces can quickly degrade the seal lip and lead to leaks. Regular monitoring and replacing worn-out seals before they fail can significantly enhance the machinery's lifespan and reliability.
In conclusion, oil seals are the unsung heroes in machine operations, safeguarding against leakage and contamination. By choosing the appropriate type for your specific needs and maintaining them proactively, you ensure smooth operations, enhance equipment longevity, and uphold your industry reputation for reliability and safety. Whether you operate in automotive, industrial, or specialized fields, mastering your understanding of oil seals is a pivotal step towards operational excellence.