Enhancing machinery longevity and performance, oil seals play an indispensable role in numerous industrial applications. Despite their small size, they are crucial to ensuring that lubrication systems function efficiently. An oil seal, often referred to in technical documentation as a radial lip or rotary shaft seal, is designed to close spaces between stationary and moving components in mechanical equipment. This prevents leakage of lubricants and ingress of impurities such as dirt or moisture, which could compromise the equipment’s operation.
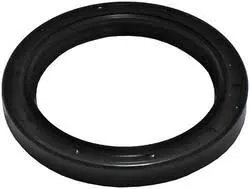
The right selection of oil seals can dramatically influence the reliability and efficiency of machinery. At the core of an oil seal is the sealing element, typically crafted from materials like nitrile rubber (NBR), fluorocarbon (FKM), or silicone. Each material offers distinct advantages; for instance, NBR provides excellent resistance to petroleum oils and hydraulic fluids, while FKM offers superior resistance to high temperatures and chemical attack. Consequently, understanding the operating environment is essential before selecting an oil seal material.
In practice, industry experts recommend considering factors such as temperature, speed, pressure, and environmental exposure when choosing oil seals. A seal designed for high-speed rotary applications, for example, may not be suitable for static compression applications. Furthermore, variables like the concentricity of the shaft and housing bore, surface finish, and shaft hardness should be evaluated to optimize seal lifecycle and performance.
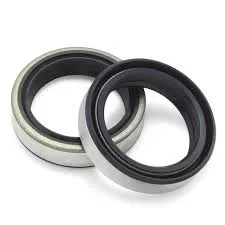
Authoritative guidelines from industry bodies like the Society of Automotive Engineers (SAE) and the International Organization for Standardization (ISO) provide detailed specifications and testing methods for oil seals, ensuring consistency and reliability across applications. A precise review of these standards often unveils insights into best practices for seal installation and maintenance, a crucial factor in mitigating premature seal failure.
oil seal pdf
Trust in oil seal performance is further bolstered through rigorous testing. Field experiences from engineers have shown that regular wear and tear checks and timely replacements significantly increase overall machinery uptime. Case studies highlight that the incorrect installation or misalignment of an oil seal can lead to unexpected downtimes and hefty repair costs, underlining the vital need for expertise during installation.
Professionals suggest maintaining a comprehensive database of equipment performance metrics, which can help in predictive maintenance schedules and foreseeing potential seal issues before they culminate into failures. With digital advancements, many enterprises leverage AI-driven predictive analytics tools to anticipate maintenance needs, effectively bridging the gap between seal performance and machine reliability.
Ultimately, the integration of a suitable oil seal is not just a matter of sealing off lubricants; it’s about optimizing the entire operational efficiency of an equipment piece. By investing in high-quality seals and adhering to robust maintenance protocols, businesses can ensure enhanced equipment longevity and performance, thereby achieving a sustainable advantage in a competitive industrial landscape.
The strategic implementation of oil seals, backed by expert recommendations and authoritative standards, assures not only operational efficiency but also fortifies a company’s commitment to quality and reliability, thus earning the trust of stakeholders and advancing industry benchmarks.