Floating oil seals, also known as duo cone seals or mechanical face seals, are critical components in heavy machinery, particularly in equipment used in harsh environments such as construction, agriculture, mining, and forestry. These seals play a fundamental role in preserving the longevity and performance of equipment by preventing the ingress of external contaminants like dirt, water, and abrasive particles, while simultaneously retaining lubricants within rotating assemblies.
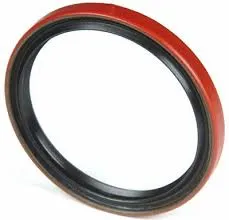
The construction of floating oil seals is robust and meticulously engineered to withstand the extreme conditions typical of industrial settings. They are primarily composed of two metal seal rings and two flexible rubber rings that act as secondary seals. The metal rings, often made from rugged materials such as cast iron or steel, are precision-ground to ensure a perfect fit and optimal sealing under varying operational conditions. This careful crafting is essential for maintaining functionality, reducing downtime, and cutting maintenance costs, which is a crucial consideration in high-demand industrial operations.
Experience in the field suggests that the selection and application of floating oil seals should not be underestimated. The efficacy of these components can greatly influence the maintenance schedule and lifecycle of the machinery. Leading industry experts stress the importance of choosing seals that are appropriate for the specific operating conditions of the application. Factors such as temperature fluctuations, exposure to abrasive materials, chemical compatibility, and axial and radial movements must be thoughtfully assessed. Consulting with manufacturers or experienced engineers can provide invaluable insights, ensuring that the chosen seal configuration delivers optimal performance and reliability.
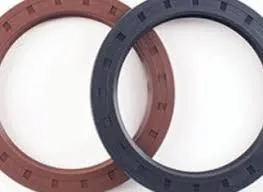
On a more practical level, the installation and maintenance practices concerning floating oil seals are key determinants of their success in extending the life of equipment.
Proper installation is crucial, as misalignment or improper fitment can lead to premature failure and costly repairs. Regular inspection and timely replacement are recommended to avoid unexpected breakdowns. Technicians and maintenance personnel are advised to follow manufacturer guidelines and utilize appropriate tools during installation to avert damage to the seals and associated components.
floating oil seal
The expertise involved in designing floating oil seals is a testament to the engineering prowess that goes into ensuring these components provide substantial value. Manufacturers invest heavily in research and development to advance seal technology, focusing on enhancements such as improved material compositions, innovative design features, and advanced manufacturing techniques. These advancements serve to increase the operational lifespan and reliability of seals, cater to more demanding applications, and consequently offer businesses a robust return on investment.
Authoritativeness in the field of floating oil seals can be attributed to their widespread adoption and proven performance across various industries. Case studies and real-world applications consistently underscore their critical role in maintaining the operational integrity of heavy machinery. Industry leaders often highlight success stories where the deployment of high-quality mechanical face seals has directly contributed to enhanced equipment efficiency and significant cost savings.
Trustworthiness is another vital aspect of floating oil seals. Top-tier manufacturers stand behind their products with comprehensive warranties and provide extensive technical support to assist customers in selecting, installing, and maintaining seals that meet their specific needs. Additionally, rigorous testing regimens, including endurance and environmental tests, are conducted to ensure that these seals surpass industry standards. This commitment to quality and support bolsters the confidence of end-users in their machinery's continuing performance and reliability.
In conclusion, floating oil seals are indispensable in maintaining the optimal performance and durability of heavy-duty machinery. Their design and engineering are paramount to preventing contamination and preserving lubricant integrity, ultimately protecting vital machine components. Through experienced selection, proper installation, and diligent maintenance, these seals are a trusted ally in maximizing equipment uptime and minimizing operational costs. Therefore, for industries reliant on heavy machinery, investing in quality floating oil seals is not merely a choice but a necessity for prolonged success and efficiency.