Installing oil seals is a critical process that directly impacts the performance and longevity of machinery in various industrial applications. With decades of expertise in mechanical engineering and maintenance, we are committed to sharing insights that ensure precision and reliability in seal installation. This article aims to guide you through the nuances of oil seal installation, backed by professional knowledge and tested techniques that promise effective results.
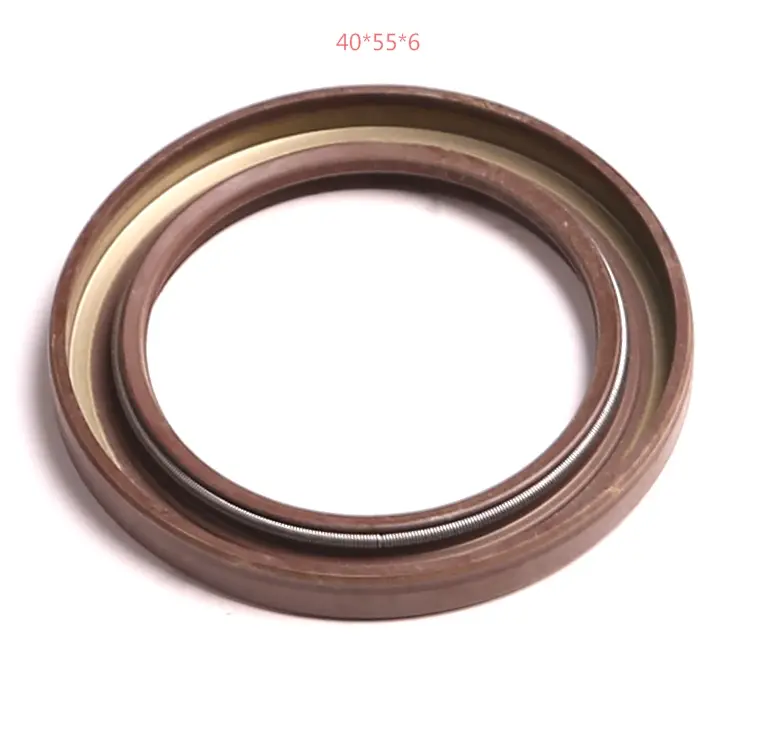
To begin with, understanding the core functionality of an oil seal is crucial. Oil seals are designed to keep lubricants within the assembly while preventing contaminants from entering. This dual function minimizes friction and wear, leading to increased efficiency and reduced mechanical failures. Selecting the right oil seal involves evaluating factors such as material compatibility, temperature range, shaft speed, and pressure conditions. These considerations are pivotal to ensuring the seal remains effective under operational stresses.
Preparation is paramount in the installation process. Thoroughly clean the housing and shaft to remove any residues, as contamination can lead to seal damage. Inspect both the shaft and housing to verify there are no aberrations or dents that may compromise the seal's integrity. Employing precision measuring tools such as micrometers can aid in confirming that dimensions are within the tolerances specified by the seal manufacturer.
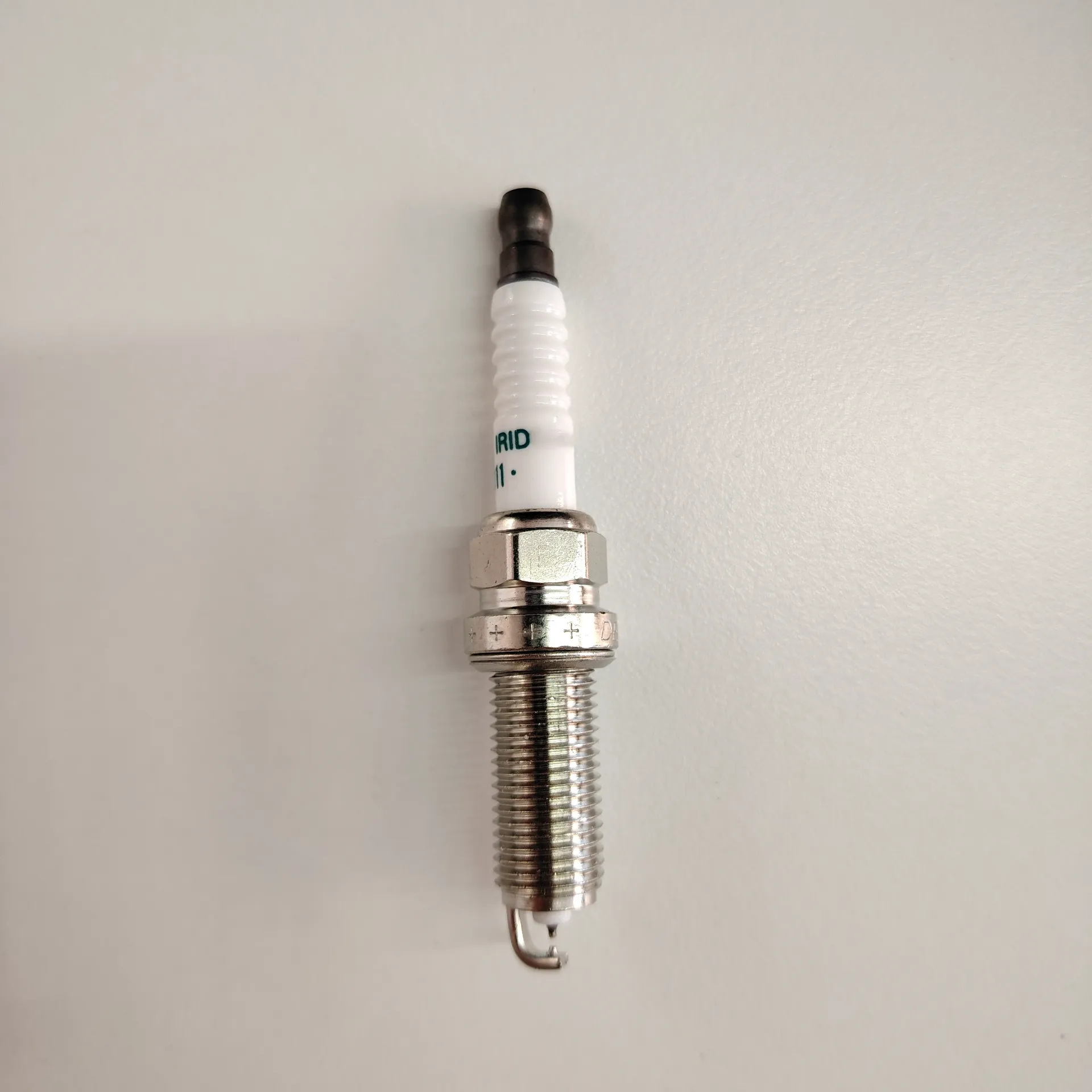
A common pitfall during installation is improper handling, which can cause irreversible damage to the seal lip. Always use dedicated tools such as seal drivers or press tools specifically designed for oil seals. These tools facilitate an even application of force, ensuring the seal installs uniformly and reduces the risk of distortion. Additionally, apply a thin layer of lubricant to the seal and shaft; this not only eases the installation process but also provides initial lubrication to reduce dry friction upon start-up.
installing oil seals
Aligning the oil seal correctly with the shaft is another critical step. An improper alignment can lead to premature wear or leakage. Install the seal perpendicularly to avoid cocking, ensuring its lip contacts uniformly around the shaft. In dynamic applications, it's advisable to rotate the shaft gently while pressing the seal into place. This action helps in correctly seating the lip and evenly distributing lubricant.
Post-installation inspection is equally important. Verify that the seal is seated flush against the housing and ensure there is no visible distortion. A pressurized leak test, where applicable, can be an effective way to confirm the integrity of the seal in maintaining the desired lubrication levels without leak paths. Additionally, monitoring performance metrics such as temperature readings and vibration analysis post-operation can provide early insights into potential failures, allowing for proactive maintenance.
Finally, maintaining a logbook of installations can boost the credibility and authoritativeness of your practices. Documenting each installation including specifications, environmental conditions, and any anomalies encountered can serve as a valuable resource for future reference or troubleshooting.
In conclusion, while the process of installing oil seals may seem straightforward, it demands meticulous attention to detail and adherence to best practices to achieve optimal functioning. Drawing from industry experience and expertise, following these guidelines will augment the effectiveness and reliability of oil seal installations, ultimately leading to enhanced equipment performance and extended service life.