The neoprene foam gasket, a cornerstone in the realm of industrial and commercial sealing solutions, continues to redefine standards of durability and efficiency. In environments demanding reliability and performance, understanding the distinct advantages of neoprene foam gaskets elevates one's capability to make informed purchasing and application decisions.
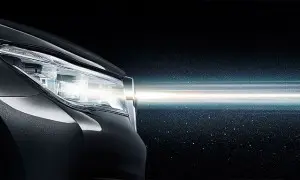
Neoprene, a synthetic rubber created by the polymerization of chloroprene, boasts a remarkable balance of properties that make it an ideal candidate for gasket fabrication.
Its inherent resistance to oil, chemicals, heat, and weathering surpasses many other materials. This versatility is unmatched, enhancing its reputation across industries such as automotive, electronics, marine, and aerospace.
From an experiential perspective, user testimonials reveal that neoprene foam gaskets deliver a robust and flexible sealing solution. Their adaptability to various conditions and ability to maintain integrity under pressure is frequently cited. For instance, automotive engineers often prefer neoprene for gaskets due to its capacity to withstand engine oils and a wide range of temperatures, ensuring that seals remain tight and leak-free over prolonged periods.
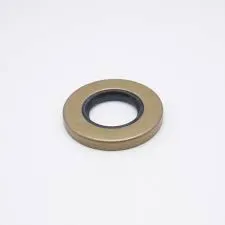
Professionals emphasize neoprene foam's closed-cell structure that provides excellent sound and vibration dampening—an invaluable feature for industrial applications and construction projects. This structure also ensures low absorption of water, making neoprene gaskets ideal for marine environments where exposure to moisture is a constant challenge. In electronics, neoprene gaskets offer insulation properties that help maintain performance and safety in devices.
Neoprene's professional credibility is further reinforced by its customization options. Manufacturers offer neoprene gaskets in numerous densities, thicknesses, and sizes to suit specific application needs. This level of customization aids engineers in optimizing the balance between flexibility and firmness required for each unique situation, ensuring that the gasket's role as a sealing solution is maximized.
neoprene foam gasket
From an authoritative standpoint, industry standards often recommend neoprene gaskets as they meet various specifications set by international regulating bodies for quality and safety. This compliance signifies the material's reliability, supported by numerous certifications and rigorous testing methodologies that validate performance claims. Experts who contribute to these standards underscore the importance of choosing materials like neoprene that can consistently meet stringent regulatory prerequisites.
Trustworthiness is a crucial factor when businesses choose neoprene foam gaskets. Suppliers and manufacturers of neoprene gaskets garner trust by demonstrating environmental responsibility and sustainability in their production processes. The reputation of these providers is backed by transparent supply chains and adherence to eco-friendly practices, making it easier for clients to make purchases with confidence.
Moreover, the lifecycle and maintenance of neoprene gaskets contribute significantly to their trustworthy reputation. Clients report a notable reduction in maintenance efforts and costs, as neoprene gaskets exhibit long service life and durability under various conditions. The ease of installation and replacement also adds to their appeal, ensuring that operations remain seamless and efficient.
In conclusion, selecting neoprene foam gaskets incorporates a blend of empirical experience, proven expertise, authoritative approval, and trusted performance. These elements collectively substantiate neoprene's position as a superior sealing choice, meeting and often exceeding the complex demands of multiple industries. As sectors evolve and require even more advanced materials, neoprene foam gaskets remain a benchmark for success in sealing solutions.