The Indispensable Role of Oil Seal Rubber in Modern Industry
In the realm of mechanical engineering and industrial manufacturing, oil seal rubber plays an integral part in ensuring efficient machinery operation and preventing fluid leakage. This seemingly humble component is a testament to the power of combining functionality with durability, and its significance cannot be overstated.
An oil seal, primarily constructed from rubber, is a vital sealing device designed to prevent the ingress of contaminants and the egress of lubricants or other fluids. The rubber material, chosen for its unique properties, forms the core of this seal, providing a flexible barrier that adapts to various surfaces and withstands harsh conditions.
The rubber used in oil seals is typically a synthetic blend, often a combination of nitrile butadiene rubber (NBR), fluoroelastomer (FKM), or silicone rubber, each with its own set of advantages. NBR, for instance, boasts excellent resistance to oils and fuels, making it ideal for automotive applications. FKM, on the other hand, is more resistant to high temperatures and chemicals, finding its use in aerospace and chemical processing industries. Silicone rubber, with its wide temperature range tolerance, is commonly employed in food and medical industries.
The design of oil seal rubber is a fine balance between flexibility and strength. It needs to be soft enough to conform to the mating surfaces and create a tight seal, yet robust enough to resist wear and tear, pressure, and temperature fluctuations. The rubber compound is often reinforced with materials like steel or fabric to enhance its mechanical strength and durability The rubber compound is often reinforced with materials like steel or fabric to enhance its mechanical strength and durability
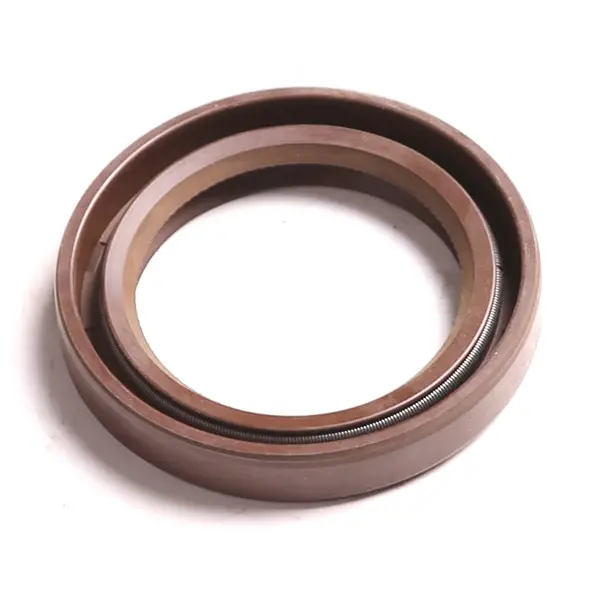
The rubber compound is often reinforced with materials like steel or fabric to enhance its mechanical strength and durability The rubber compound is often reinforced with materials like steel or fabric to enhance its mechanical strength and durability
oil seal rubber.
In operation, oil seal rubber ensures that machinery runs smoothly by maintaining the integrity of the lubrication system. By preventing oil leaks, it not only safeguards the environment but also extends the lifespan of equipment by reducing the need for frequent maintenance and replacement. Furthermore, it shields sensitive components from contamination, thereby improving overall system performance.
Despite its simplicity, the role of oil seal rubber is critical in industries ranging from automotive to aerospace, from manufacturing to food processing. Its effectiveness lies in its ability to adapt, protect, and endure in a multitude of environments and conditions. As technology advances, so does the development of more specialized and advanced rubber compounds, further solidifying the position of oil seal rubber as an indispensable element in modern industry.
In conclusion, the humble oil seal rubber, with its versatility and resilience, is a silent hero in the world of machinery. Its role, though often overlooked, is crucial in maintaining the smooth operation of countless systems and processes. As we continue to rely on technology for everyday life, the importance of oil seal rubber in ensuring reliable and efficient machinery will only continue to grow.