Navigating the world of machinery and automotive components, the term oil seal 100x120x12 often comes up among professionals who deal with the maintenance and performance optimization of mechanical systems. These oil seals play a crucial role in maintaining the smooth operation of equipment, which can often be underestimated by those not familiar with the intricacies of mechanical engineering.
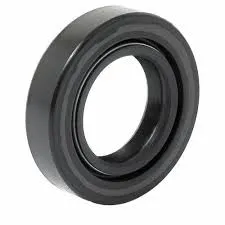
Oil seals, commonly referred to as rotary shaft seals or radial lip seals, are pivotal in preventing lubricant leakage. They also serve as a barrier to prevent contaminants from entering the machine systems, which can otherwise lead to substantial damage and inefficiency. The dimensions of the oil seal,
100x120x12, indicate its internal diameter, outer diameter, and thickness in millimeters. This specific size is often used in a range of applications including automotive engines, gearboxes, and industrial machinery.
Real-world Experience Technicians and engineers often encounter the need for an oil seal replacement when servicing an engine that shows signs of oil leaks. A sealed environment ensures that the mechanical system retains its lubricants and operates with minimal friction, which is essential for the longevity and reliability of the equipment. The size 100x120x12 is frequently utilized in heavy-duty machinery where precision and reliability cannot be compromised. One expert spoke of a cement plant where improper sealing led to the contamination of lubricant systems with dust and debris, causing severe wear and tear on expensive gearboxes. The subsequent retrofitting with high-quality oil seals fitting the 100x120x12 dimensions rectified the issue, leading to enhanced operational efficiency and reduced maintenance downtime.
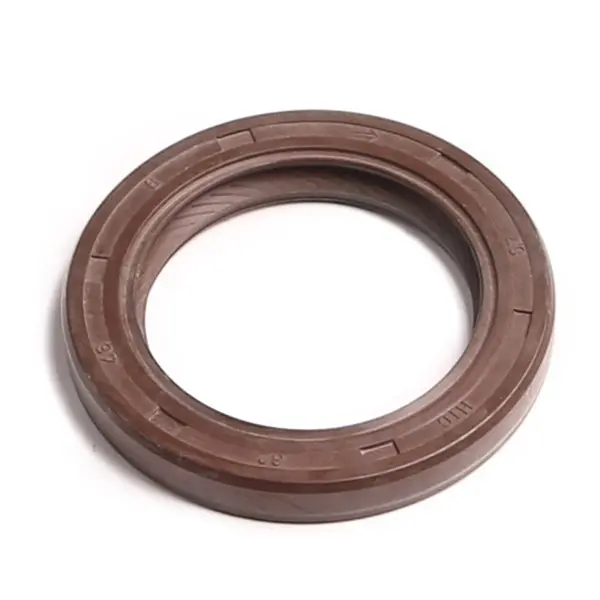
Expertise Precision manufacturing of the oil seal is vital. It involves selecting materials that can withstand harsh conditions, such as varying temperatures and exposure to industrial chemicals. Nitrile Rubber (NBR) and Fluoroelastomer (FKM) are commonly employed materials due to their exceptional resistance to oils and their ability to maintain structural integrity over a wide temperature range. The manufacturing process also includes meticulous quality control to ensure that the dimensions are exact, ensuring a snug fit within the machinery which is crucial for its effectiveness.
oil seal 100x120x12
Authoritativeness Trusted manufacturers engineer these oil seals with exacting standards to cater to high-performance expectations. Companies with ISO certifications assure that their production processes meet international quality standards. Such credentials provide confidence to purchasers and users alike, as they signify a commitment to excellence and adherence to stringent methodologies in making products that are reliable and robust.
Trustworthiness When selecting an oil seal, particularly one with dimensions like 100x120x12, it’s crucial to consider the reputation of the supplier and manufacturer. Feedback and reviews from previous buyers who have practical experience with the product in similar applications can provide valuable insights. High ratings often correlate with long-lasting performance and reliability. Furthermore, buying from suppliers who provide a warranty or guarantee on their products can provide additional peace of mind, as this reflects the confidence they have in their seals’ ability to perform as promised.
In a world where machinery efficiency is paramount, selecting the right components can make a significant difference. Expertise in understanding the application requirements and selecting products from authoritative manufacturers lead to trustworthy and high-performing solutions. The oil seal dimension of 100x120x12 is more than just a number; it is a specification that speaks to the demands of high-stakes industrial environments. While they may seem insignificant when compared to larger machine parts, oil seals are indeed the unsung heroes that ensure machines run smoothly and efficiently without unexpected breakdowns. Trustworthy products contribute not only to the smooth operation of individual machines but also to the profitability and sustainability practices of enterprises by minimizing unnecessary resource wastage and production downtimes.