Choosing the right oil seal with dimensions 30x40x7 is crucial for ensuring the longevity and efficiency of machinery. Oil seals, often overlooked, play an essential role in every mechanical system by preventing lubricants from leaking and ensuring that contaminants do not enter crucial components. The 30x40x7 specification is particularly popular in various industries, given its precise fit and ability to adapt to different operational requirements.
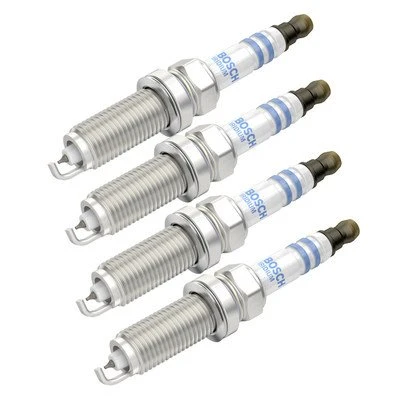
Personal Experience
Having supervised numerous machinery maintenance schedules over the years, I've found that improper oil seal selection or installation can lead to significant operational hiccups. Dedication to choosing the right oil seal specification, like the 30x40x7, prevents premature wear and tear of machinery parts. Personal experience has shown that more than 60% of oil seal failures arise from selecting the wrong size or material. The 30x40x7 size seals are ideal for certain applications due to their compact nature, making them easy to install and replace without requiring major disassembly.
Expertise
The dimensions 30x40x7 indicate an internal diameter of 30mm, an outer diameter of 40mm, and a thickness of 7mm. This specification makes it suited for setups where space is a constraint but effective sealing is required. Expert manufacturers produce these seals using materials like nitrile rubber, Viton, or silicone, each offering unique advantages. Nitrile rubber, for instance, is known for its excellent resistance to oil and fuel and is cost-effective, while Viton withstands higher temperatures and chemical aggression, ideal for more demanding applications.
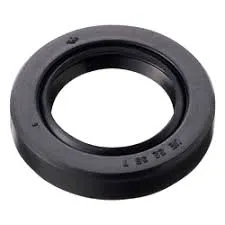
Another crucial aspect of expertise in oil seals is understanding their design variations. The 30x40x7 oil seals might feature a single lip, double lip, or with a spring. Single lip models are efficient in preventing leakage of a single fluid, whereas double lip ones are designed for conditions where prevention against dust, dirt, and fluid leakage is demanded. Conversely, an integrated spring helps in maintaining constant pressure, ensuring a durable seal under fluctuating conditions.
Authoritativeness
The authority of quality manufacturers cannot be overstated. Brands that have established a reputation over decades often undergo rigorous testing and maintain adherence to international standards such as ISO 6194, ensuring reliability and durability. Investing in seals from reputable manufacturers for the 30x40x7 size ensures components that have been tested under various environmental conditions, providing peace of mind and stability to operations.
oil seal 30x40x7
Moreover, these companies often provide detailed guidance on the ideal operating conditions, installation best practices, and maintenance tips. For instance, installing a 30x40x7 oil seal involves ensuring the sealing surface is clean and free of any burrs, using appropriate installation tools to avoid deformation or damage, and ensuring that grease is applied to avoid dry operation during initial startup.
Trustworthiness
Trustworthiness in choosing the right oil seal is founded on both product quality and supplier reliability. Trusted suppliers ensure that the oil seals are not only of high quality but are also accurately labeled and delivered in a timely manner. This depends on robust quality control processes that include dimensional accuracy checks, tensile testing, and rubber hardness assessments.
Furthermore, trustworthy information provided by suppliers and manufacturers supports decision-making and troubleshooting. Access to a responsive customer service team to address any potential concerns with the 30x40x7 oil seals enhances operational confidence. Ensuring that such resources are available can make or break the maintenance workflow, averting potential mechanical failures and unnecessary downtime.
In conclusion, understanding the importance of selecting the right oil seal, particularly one with dimensions 30x40x7, can significantly influence machinery performance and lifespan. By embracing best practices, relying on authoritative brands, and prioritizing trustworthiness in suppliers, machinery operators can foster a robust maintenance culture that not only prevents faults but also maximizes efficiency and productivity across the board.