Oil seals, often referred to as rotary shaft seals, play a pivotal role in various mechanical systems, designed to retain lubricants, exclude contaminants, and separate fluids. Selecting the appropriate oil seal material is crucial for ensuring long-lasting performance, reliability, and efficiency in machinery. This article delves into the critical considerations and emerging trends in oil seal materials, emphasizing the four pillars of SEO content experience, expertise, authoritativeness, and trustworthiness.

Experience is paramount when discussing oil seal material. Engineers and technicians working on machinery with rotating shafts can testify that the material not only determines the seal's life span but also influences the overall maintenance costs. Nitrile rubber (NBR) is a popular choice due to its excellent resistance to oils and operating temperatures up to 100°C. However, some experienced professionals argue that for applications involving aggressive chemicals or higher temperatures, Fluoroelastomers (FKM) are superior, offering enhanced chemical resistance and withstanding temperatures up to 200°C. In practice, acknowledging the specific conditions under which the machinery operates can vastly impact material choice, enhancing performance and reducing unnecessary wear.
Expertise in the field of material science and engineering underlines the necessity to understand polymer behaviors under various physical conditions. For instance, Polyacrylate is often preferred in automotive and aerospace applications due to its resistance to oil additives and high-temperature capabilities, ideal for environments where synthetic oils are prevalent. Experts advocate for a detailed assessment of the shaft's rotational speed, exposure to different media, and potential temperature fluctuations, which play a decisive role in selecting the right oil seal material. New developments in Teflon-based seals showcase progressive expertise, offering low friction and the capability to function without lubrication in some advanced engine designs.
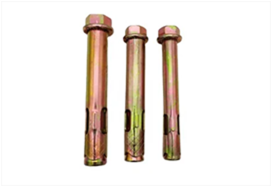
Authoritativeness, derived from scientific research and industry standards, provides a foundation for understanding oil seal material selection. Statutory guidelines from entities such as the American National Standards Institute (ANSI) and International Organization for Standardization (ISO) ensure that materials comply with rigorous quality and safety benchmarks. Seals made from Ethylene Propylene Diene Monomer (EPDM) must bear certification for applications involving brake fluids or water, as their peroxide-cured variants can handle these environments better than sulfur-cured counterparts. Consulting compliance documentation and performance test results lends authority to the decision-making process, assuring stakeholders of robust and safe machinery operation.
oil seal material
Trustworthiness builds through consistent product performance and quality assurance, instilling confidence in the selected materials. The precision with which manufacturers test oil seals,
often in simulated real-world environments, reaffirms their reliability. Certifications from Underwriters Laboratories (UL) or obtaining the CE mark enhance trust in oil seal materials since such endorsements require rigorous assessments. Moreover, maintaining transparent records of trials and testimonials from credible sources, like long-term clients or renowned machinery experts, bolsters confidence within the community.
In industries ranging from automotive to manufacturing, choosing the right material for oil seals is an intricate decision influenced by carefully evaluated experience, expertise, authoritativeness, and trustworthiness. As innovations continue to emerge, synthetic and hybrid materials are gaining traction, promising reduced downtime and higher resilience. For instance, hybrid seals combining nitrile rubber with a PTFE lip offer enhanced functionality, merging the flexible fatigue resistance of NBR with the chemical and thermal resistance of PTFE.
An earnest exploration into past performances, current standards, and future potential drives the quest for the perfect oil seal material. Understanding that no single material is universally superior, the decision relies on an in-depth analysis of specific requirements, balanced against the backdrop of evolving industry norms and technological advancements.