Oil seals, pivotal components in a myriad of industrial applications, are often underestimated until their absence or failure leads to significant machinery breakdowns or inefficiencies. These petite yet powerful seals act as protective barriers, preventing the leakage of lubricants and the ingress of contaminants, thereby ensuring the longevity and optimal performance of equipment across industries—from automotive to aerospace. Understanding their technical specifications, selection criteria, and maintenance procedures is crucial for engineers and industry professionals aiming to optimize machinery performance.
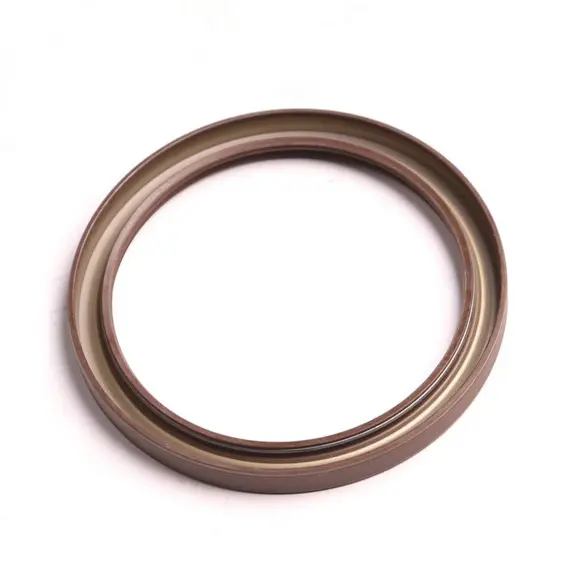
First and foremost, the selection of oil seals should be grounded on three primary parameters the nature of the application environment, the type of fluid retained or excluded, and the shaft speed. Environmental factors such as temperature extremes, exposure to chemicals, and presence of debris dictate the choice of materials—from nitrile rubber in moderate conditions to Viton in high-temperature applications. The compatibility of the seal material with the retained fluid—be it mineral oil, synthetic oil, or another lubricant—is equally critical, as chemical incompatibility can lead to rapid degradation.
The functionality of an oil seal hinges on its design—typically comprising a metal outer casing, an inner lip, and a garter spring. The design ensures that the seal maintains contact with the rotating shaft, despite axial or radial deflections. This flexibility is buttressed by the garter spring, which maintains consistent pressure, preventing leaks. Engineers often face the choice between single lip and double lip designs, the latter providing an additional barrier against contaminants, thus enhancing the seal's lifespan in grueling conditions.
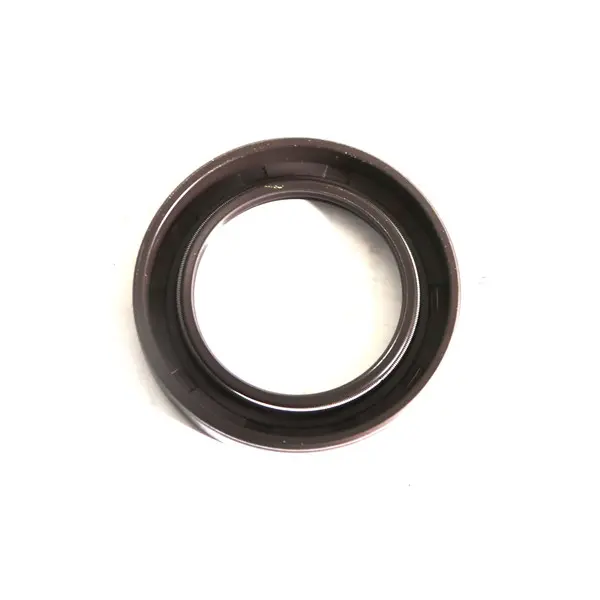
Expertise in the installation process is paramount to maximizing an oil seal's efficacy and durability. Critical to the installation is ensuring that both the seal and the shaft are impeccably clean, devoid of any nicks or debris that could compromise the seal. The process should ideally be conducted using purpose-designed tools that ensure the seal is inserted evenly, avoiding deformation. Post-installation, a thorough inspection is advisable to verify that the seal is seated correctly and there are no visible signs of damage.
oil seals
Regular maintenance and timely replacement form the backbone of sustaining oil seal integrity and machinery efficiency. Inspections should focus on detecting leaks, signified by oil seepage or accumulated grime around the seal. Such symptoms, if observed, necessitate prompt addressing to prevent exacerbation, potentially safeguarding against expensive repairs or operational downtime. Advanced techniques such as predictive maintenance using vibration analysis and thermal imaging can preemptively identify seal wear and tear, facilitating scheduled replacements that dovetail with operational cycles.
For professionals vested in leveraging the full potential of oil seals, continuous education and staying abreast of technological advancements are imperative. Modern innovations—such as seals with enhanced elastomers, optimally engineered lip designs, and coatings that reduce friction—offer tangible benefits in extending seal life and enhancing performance. Collaboration with manufacturers for custom solutions tailored to specific operational profile demands can yield significant returns, both in equipment reliability and cost efficiencies.
Ultimately, the authority on oil seals rests not only on academic knowledge but also on real-world application and experience. Industry veterans often draw from a repository of troubleshooting methodologies, understanding nuances that may escape novices. A culture of knowledge sharing—through workshops, webinars, and cross-industry forums—helps cultivate a community that values precision, sustainability, and performance excellence.
In summary, oil seals are an unassuming yet critical element in enhancing industrial machinery's reliability and efficiency. Selection, installation, and maintenance—each embodies principles that, when adhered to, align with the broader goals of minimizing friction, maximizing lifespan, and safeguarding assets. For those invested in operational excellence, oil seals are not merely components but pivotal allies in the quest for industrial sustainability and innovation.