Understanding the intricacies of oil seals by dimension is crucial for industries where equipment reliability and longevity are paramount. These seemingly simple components play a profound role in machine performance, preventing harmful contaminants from entering systems and maintaining lubrication. For those seeking guidance on how to leverage oil seal dimensions effectively in their applications, several factors come into play, blending experience, expertise, authoritativeness, and trustworthiness.
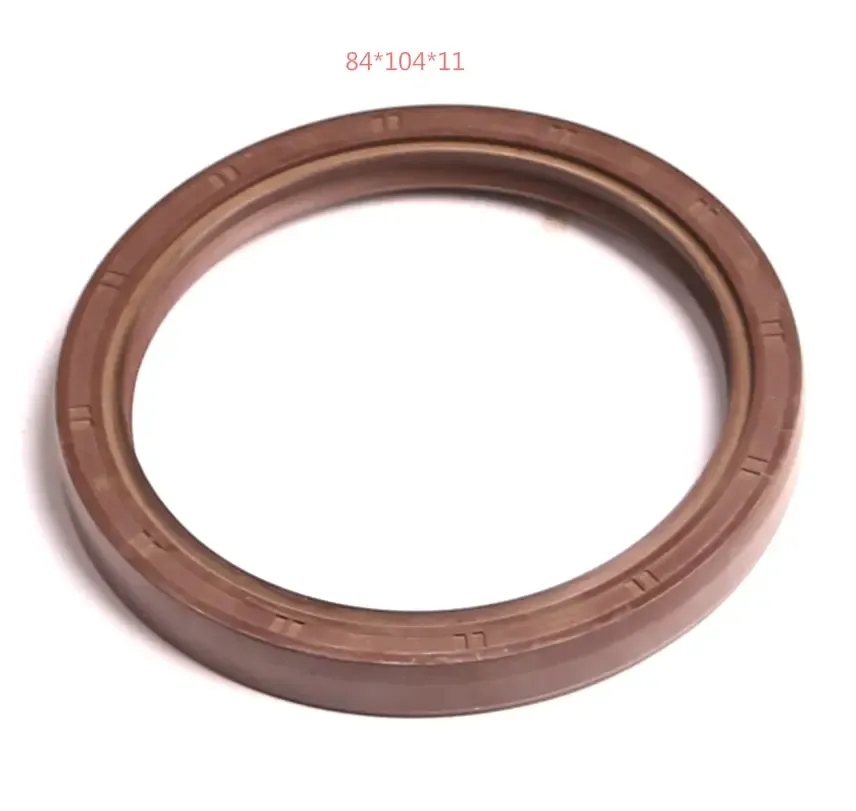
At the core of selecting the right oil seal by dimension lies an understanding of the seal's purpose within an application. Oil seals, often referred to as rotary shaft seals, are designed to close spaces between stationary and moving components in mechanical equipment. This function is critical, as it helps in safeguarding the integrity of the machinery by preventing the leakage of lubricants and entry of contaminants like dirt, dust, and moisture.
Industry experts emphasize the importance of precise measurements when it comes to oil seals. An accurate understanding of the dimensions — including the inner diameter (ID), outer diameter (OD), and width — is indispensable for ensuring a proper fit. These measurements determine not only the compatibility of the seal with the shaft and housing but also influence its performance and lifespan. Utilizing calipers and micrometers to measure these dimensions carefully will yield the best results, enabling the selection of a seal that meets the specific requirements of an application.
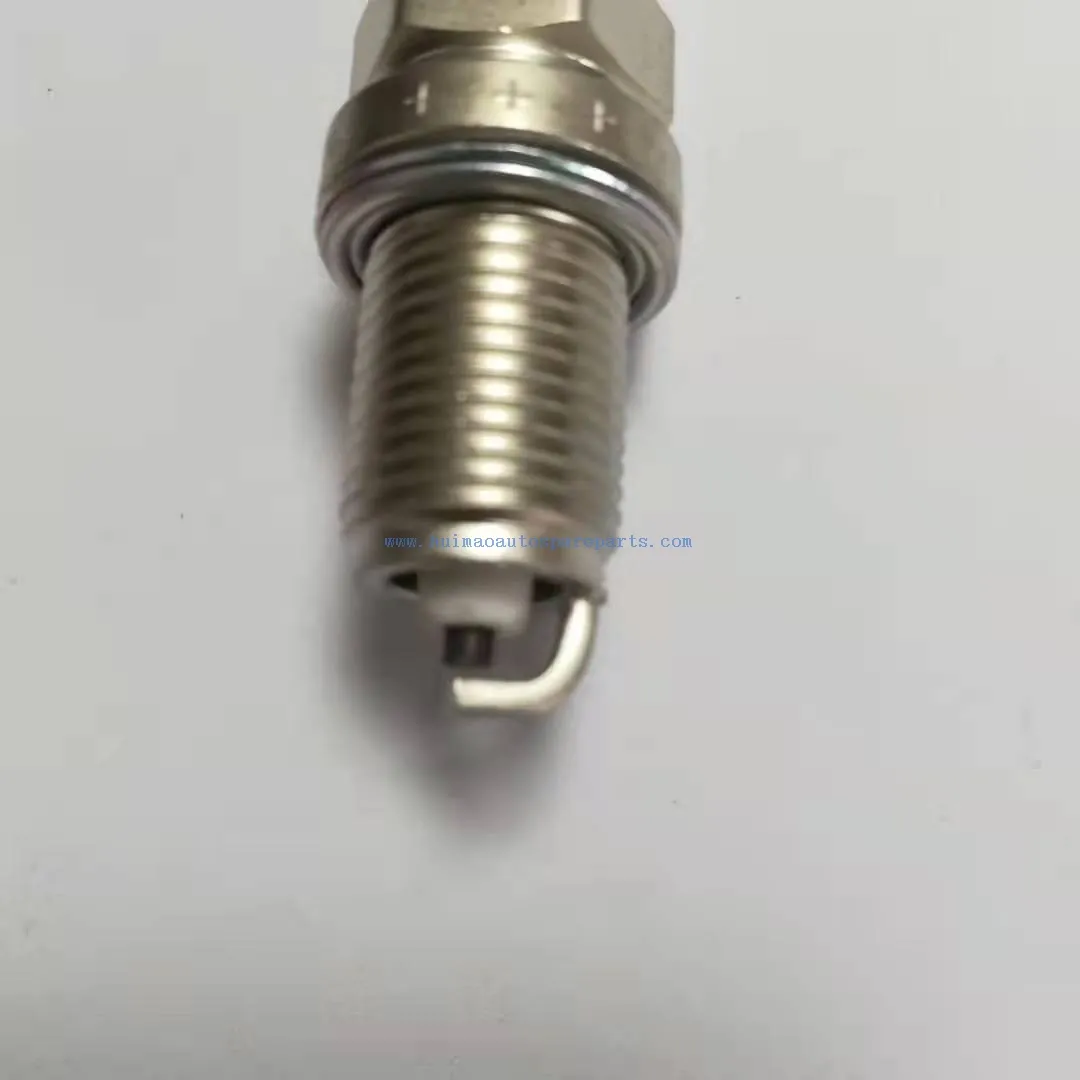
When it comes to materials, there is no one-size-fits-all solution. Different applications demand seals made of materials that can withstand specific environmental conditions such as extreme temperatures, chemical exposure, or varying pressures. Rubber materials like nitrile, silicone, and fluorocarbon offer different degrees of resistance to various media and temperatures. Industry leaders suggest performing a thorough analysis of the application's operating environment to determine the most suitable material for the oil seal, thereby ensuring durability and functionality.
Experts also recommend considering the seal's lip design. The lip is the critical component that interfaces with the shaft. Single lip seals might suffice for applications with minimal contamination risks, whereas double lip seals offer enhanced sealing against high-pressure environments or significant exposure to contaminants. For high-quality performance, the seal tension must align with shaft rotation speed and pressure conditions, a task best handled by consulting with seasoned professionals or adopting industry-standard guidelines.
oil seals by dimension
The nuances of installing oil seals can not be overlooked. An improper installation negates the benefits of appropriate dimensioning and material selection. Misalignment, excessive force, and incorrect tool usage are pitfalls easily avoided with adequate training and guidance from authoritative sources. A trusted approach involves regularly reviewing manufacturer guidelines, ensuring that the installation process enhances seal accuracy and longevity.
Regular maintenance and inspection further attest to the reliability and trustworthiness of oil seal applications. Early identification of wear and tear can prevent unexpected machinery failures. Seasoned professionals advocate for periodic evaluations of the seals, focusing on wear patterns, deformation, and hardening as indicators of seal health. Such vigilant practices, backed by expert guidance, can dramatically extend machinery life and optimize performance.
The adoption of oil seals based on precise dimensions ultimately reflects a blend of technical expertise and experience-based know-how. Involving reputable manufacturers and distributors in the decision-making process ensures alignment with the latest advancements in seal technology and best practices. These industry stakeholders bring a treasure trove of insights into tailoring solutions that perfectly fit diverse operational needs, thereby solidifying the machinery's defensive line against potential failures.
Trustworthiness in oil seal applications is about making informed, expert-backed decisions that resonate with industry standards — a sentiment echoed by industrial specialists and trusted voices alike. When reliability and efficiency stand as keystones of operational success, the conscientious application of oil seals by dimension without a doubt contributes to the well-rounded maintenance of mechanical integrity.
In summary, navigating the landscape of oil seals by dimension requires a consideration of several factors, from precise measurement to environmental compatibility, proper installation, and regular maintenance. This thoughtful approach ensures the effective protection of mechanical systems, bolstered by industry expertise and authoritative recommendations. As such, those who embark on this journey with an appreciation of these elements embrace both a proactive and knowledgeable stance towards enhancing machinery reliability and performance.