Navigating the vast landscape of plumbing supplies, one encounters countless components, but few are as pivotal and understated as the pipe rubber gasket. This small, yet crucial, component is the linchpin ensuring the effectiveness, safety, and longevity of piping systems across various industries. Its importance spans residential plumbing, industrial applications, and even high-stakes environments such as nuclear power facilities.
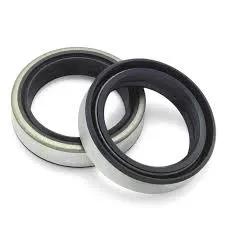
Understanding the nuances of pipe rubber gaskets begins with diving into their fundamental purpose to create a secure and watertight seal between two surfaces, preventing leaks and ensuring efficiency. This is particularly critical in systems that transport liquids or gases under significant pressure. By precisely channeling the pressure and stress across the seal's contact points, these gaskets ensure that joints remain intact and functional over diverse conditions.
The choice of material in a pipe rubber gasket is not trivial. With applications ranging from simple household pipes to complex industrial machinery, the type of rubber used can vary significantly. Generally, these gaskets are made from high-grade rubber materials like EPDM (ethylene propylene diene monomer), NBR (nitrile butadiene rubber), and SBR (styrene-butadiene rubber). Each type brings specific resistances to heat, cold, chemicals, and abrasion, catering to distinct operational environments. For instance, NBR is often preferred in oil and gas industries due to its exceptional resistance to oils and fuel, while EPDM is favored for its outstanding weather and thermal resistance, making it ideal for outdoor or high-heat applications.
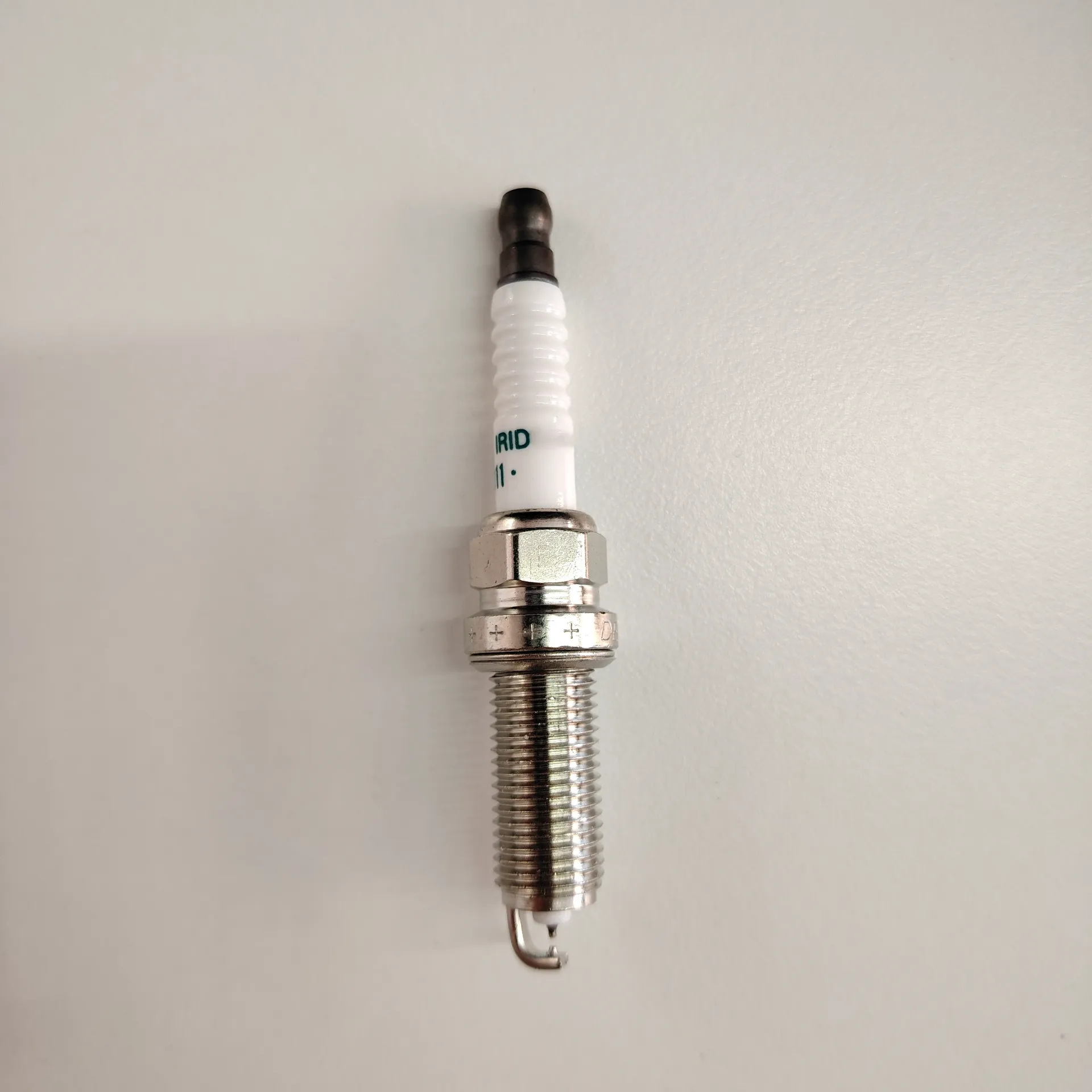
One of the pivotal attributes of rubber gaskets is their flexibility, which allows them to maintain a tight seal even as the temperature and pressure fluctuate. This adaptability ensures that, unlike rigid sealants, the gasket can accommodate expansion and contraction of materials, which is vital for long-term reliability.
In evaluating the performance of any rubber gasket, attention must be given to its compression set—a measure of the material's ability to return to its original thickness after compression. A lower compression set indicates a better performance, as the gasket will maintain its seal over time without significant deformation, thus reducing maintenance needs and extending the lifecycle of the piping system.
pipe rubber gasket
The installation of rubber gaskets, while seemingly straightforward, demands careful consideration and precision. Improper installation can lead to gasket misalignment, resulting in leaks and potential system failures. Hence, adhering to manufacturer guidelines, ensuring clean and smooth interface surfaces, and applying uniform pressure during installation are integral steps that should not be overlooked.
Choosing the right supplier for pipe rubber gaskets is equally essential. A trusted supplier should provide comprehensive data on the performance characteristics of the gaskets, including test results and compliance with industry standards. Certifications like ISO 9001 for quality management often serve as benchmarks for reliability and quality assurance in gasket manufacturing.
Looking forward,
advancements in material science promise to further enhance the performance of rubber gaskets. Innovative compounds are being developed to improve durability, thermal resistance, and chemical inertness, expanding the usability across challenging environments. Incorporating these advancements could significantly optimize operational efficiency and reduce maintenance costs, underscoring the technological stride within this seemingly simple component.
In conclusion, pipe rubber gaskets may appear inconspicuous, but they are the unsung heroes in maintaining system integrity across myriad applications. Their role cannot be overstated, and a well-informed selection, installation, and maintenance approach will ensure long-term efficiency and safety in any piping system. Whether you are a homeowner tackling a DIY project or an industrial expert overseeing large-scale operations, understanding the crucial role these gaskets play is indispensable for achieving optimal results.