In the intricate world of pneumatic and hydraulic systems, one component stands out for its pivotal role in ensuring efficiency and longevity the piston oil seal. This seemingly small component carries significant importance in the functionality and maintenance of machinery across various industries.
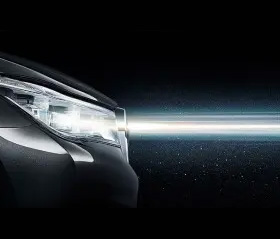
Understanding the essence of a piston oil seal begins with recognizing its purpose. At its core, a piston oil seal is designed to retain hydraulic fluid within a cylindrical system, preventing leakage and maintaining pressure. This task is of utmost importance, as any loss in fluid not only diminishes efficiency but also increases wear and tear, leading to potential system failures. A properly functioning oil seal enhances the machine's overall performance and reduces operational costs by prolonging the service intervals.
From an expert perspective, the selection of a piston oil seal requires an understanding of several key factors.
The material composition is pivotal for its functionality. Modern seals commonly use materials such as nitrile rubber, Viton, or Teflon, each offering distinct advantages. Nitrile rubber provides excellent wear resistance, making it suitable for general use. Viton offers superior chemical resistance, particularly in environments where exposure to varied fluids is expected. Teflon, with its low friction coefficient, ensures durability and performance in high-temperature contexts.

When discussing expertise in the field, installation precision cannot be overlooked. A seal improperly installed not only fails to prevent leakage but may also incur damage during operation. It's essential to follow manufacturer specifications regarding seal fitment, ensuring that the housing and shaft dimensions align accurately with the seal size. Furthermore, investing time in the correct lubrication during assembly can greatly enhance seal longevity and performance.
piston oil seal
Authoritativeness in the realm of piston oil seals is garnered through an understanding of their applications across industries. In the automotive industry, these seals are indispensable in maintaining the integrity of engine and transmission systems. They ensure that the oils do not escape their designated pathways, thereby safeguarding against contamination and component wear. In the manufacturing industry, hydraulic presses utilize piston oil seals to sustain the immense pressures required for metal forming and molding processes.
Trustworthiness is another crucial aspect when evaluating piston oil seals. This is often measured by the reliability of manufacturers and the guarantees they offer. Leading manufacturers subject their seals to rigorous testing processes, including pressure, temperature, and chemical exposure tests, to affirm their integrity and performance consistency. Diligent end users prioritize sourcing seals from reputable brands that adhere to international quality standards such as ISO, ensuring both safety and efficacy.
For those involved in the maintenance and procurement of these components, regularly scheduled inspections are vital. Even the most durable oil seals are susceptible to wear over time, more so in extreme operational conditions. Establishing a routine check-up for signs of surface wear, leakage, or any anomaly can pre-empt costly repairs by facilitating timely interventions. Reaching out to industry veterans for insights on specific seal issues can provide invaluable knowledge that transcends theoretical understanding, underscoring the value of experience sharing among professionals.
In essence, the piston oil seal, though a single component among many in a system, plays an integral role in ensuring the efficiency and prolonged life of machinery. Its impact spans from reducing operational costs to preventing critical failures, making it an indispensable part of modern machines. Mastery over the selection, installation, and maintenance of these seals not only reflects a blend of expertise, authority, and trust but also underscores a commitment to operational excellence.