Senior oil seals play a pivotal role in machinery maintenance, effectively preventing leakage and contamination, which are crucial for the seamless operation of industrial equipment. As their name suggests, senior oil seals are specifically designed for high-duty applications, ensuring maximum reliability and longevity. These seals serve as the unsung heroes in an array of mechanical systems, from automotive engines to hydraulic presses, safeguarding components by preserving lubrication and blocking harmful contaminants like dust and debris.
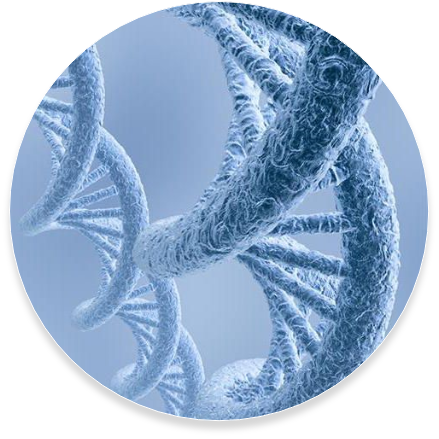
The leverage of robust materials and cutting-edge technology is fundamental to the effectiveness of senior oil seals. Manufacturers use state-of-the-art elastomers that stand up to extreme temperatures, high pressure, and aggressive chemicals, thereby enhancing the seal's durability and performance. Nitrile rubber (NBR) and fluoroelastomers (FKM) are common choices, each tailored for specific operational environments. NBR offers commendable resistance to petroleum-based oils and fuels, making it ideal for automotive applications, while FKM is preferred in scenarios requiring resistance to synthetic oils and high temperatures.
The design intricacies of senior oil seals further underscore their specialized nature. Meticulous attention is given to the seal's lip design, where precision-engineered lips ensure a tightly controlled clearance for effective fluid containment without friction-induced wear. Advances in lip technology include multi-lip configurations that provide an added layer of protection, ensuring that the primary sealing lip is always under optimal operational conditions. This design evolution is propelled by a comprehensive understanding of fluid dynamics and tribology – the science of wear, friction, and lubrication.
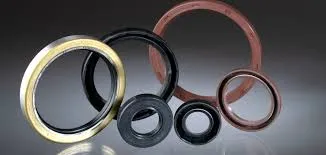
Experience across various sectors demonstrates the critical importance of selecting the right oil seal for the right application, as even the most insignificant choice can lead to major disruptions in machinery operations. Industry experts advocate for a rigorous assessment of operational conditions before selecting an oil seal, considering factors such as rotational speed, pressure, temperature, and the type of lubricant involved. Ensuring the compatibility of the seal material with the operating environment is vital for optimal performance and extended service life.
senior oil seals
Authoritative voices in the field, such as mechanical engineers and maintenance solutions consultants, often emphasize ongoing education and training in the latest developments in oil seal technology. Their guidance is instrumental in bridging the gap between theoretical knowledge and practical application. By staying abreast of technological advancements and industry best practices, professionals can ensure that machinery operates at peak performance with minimized downtime.
Trustworthiness comes from proven performance,
and case studies abound that showcase the significant impact of premium oil seals on equipment reliability. Industries ranging from automotive manufacturing to heavy machinery report reduced maintenance costs and improved operational efficiency when transitioning to superior oil seal products. These testimonials affirm the indispensable role of high-quality oil seals in extending the lifespan of machinery and preventing catastrophic failures.
In summary, senior oil seals are a specialized solution that merges advanced material engineering with precision design to deliver unmatched sealing performance in demanding applications. Their selection and usage are supported by expert knowledge and experience, ensuring they remain a trusted component in the maintenance of industrial equipment. As technology evolves, so too will the capabilities of these essential products, further solidifying their status as a cornerstone in the reliability of mechanical systems.