The shaft oil seal, often an understated component in sprawling machinery, serves as a silent guardian ensuring operational efficiency. The essence of its importance magnifies significantly within industrial realms where machinery failure is not merely an inconvenience but a critical setback, whether in manufacturing or automotive applications.
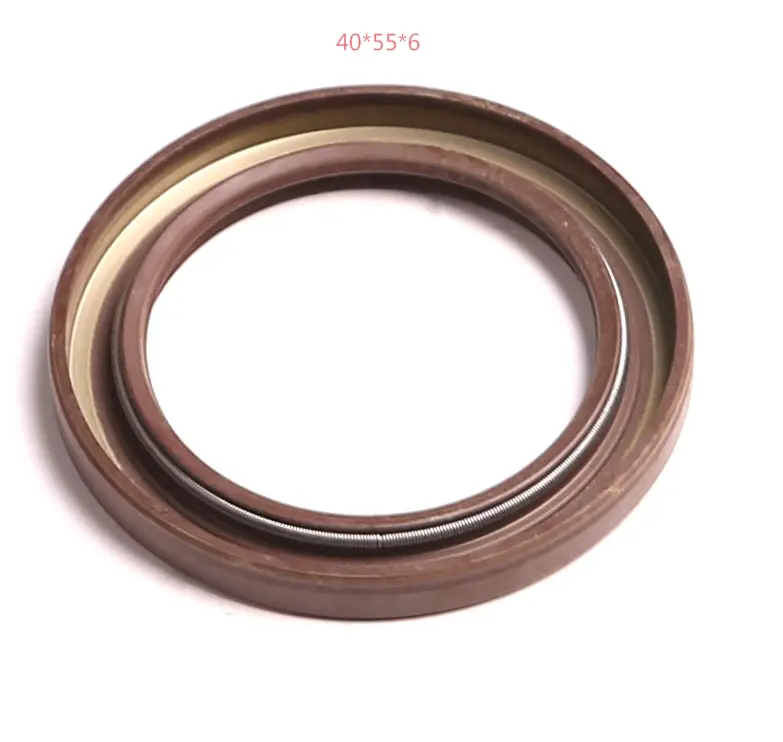
First and foremost, the design intricacies of a shaft oil seal speak volumes about its capabilities. Primarily made from reinforced rubber, PTFE, or other synthetic materials, these seals are molded to precision, incorporating elements like garter springs for added resilience. This design is not by coincidence but a culmination of years of engineering advancement aimed at providing an unyielding barrier between the internal mechanics of a machine and external elements. Reinforced materials ensure that the seal withstands immense pressures and varying temperatures, characteristics that are regularly encountered in high-functioning industrial settings.
From a professional viewpoint,
its role cannot be overstated. In typical machinery, the interaction between moving parts often generates heat and friction. The lubricants used within these environments are vital in reducing such friction, and hence, optimizing performance. A shaft oil seal preserves these lubricants within the machinery's confines, preventing leaks and contamination. It's an essential protector of the lubricant, stopping dust, dirt, and moisture from infiltrating. As evident, a compromised seal may result in lubricant leaks, leading to severe damage under continuous operation.

Anecdotal evidence from industry experts validates the efficacy of a well-functioning shaft oil seal. Experienced engineers have testified to extended machinery life often being directly correlated with the regular maintenance and timely replacement of these seals. Instances where machinery faced unexpected downtime due to overlooked seal malfunction have led to significant financial consequences, reinforcing the necessity of this component in preventive maintenance strategies.
shaft oil seal
Furthermore, the versatility of shaft oil seals is another factor underlining their significance. Their applications span across multiple sectors, from automotive and aerospace to agriculture and marine. In automotive applications, they are crucial in components such as crankshafts, where their function ensures the engine remains sealed from contaminant ingress and oil leakage, directly impacting performance and efficiency. Similarly, in agricultural machinery, where equipment is routinely exposed to harsh environments, shaft oil seals are imperative for operational integrity.
From an authoritative standpoint, choosing the right shaft oil seal requires a deep understanding of the task at hand. Consultation with specialists who possess extensive expertise in the field can yield insights into the appropriate materials and designs required for specific applications. Companies that excel in crafting these components, such as Trelleborg and SKF, continue to push boundaries in terms of innovation and durability, underscoring the importance of leveraging products from recognized leaders in shaft seal manufacturing.
Consumer trust in shaft oil seals also stems from rigorous testing and certifications. Reputable manufacturers adhere to stringent quality standards, providing assurance to end-users of product reliability. These seals are subjected to various conditions simulating real-world applications, thereby ensuring their readiness and efficacy in actual deployment.
In conclusion, the shaft oil seal may appear minor in the grand scheme of machinery components, but its impact on performance, longevity, and safety is monumental. Recognizing its critical role and investing in high-quality solutions can save industries from unplanned downtimes and facilitate seamless operations. The confluence of comprehensive knowledge, professional expertise, and trusted manufacturing processes results in shaft oil seals that not only meet but exceed operational expectations.