Tiny rubber gaskets, though small and often overlooked, play a pivotal role in a multitude of industries by ensuring that components work seamlessly together. These seemingly modest components are engineering marvels that demand a deep understanding of materials science and precise manufacturing techniques.
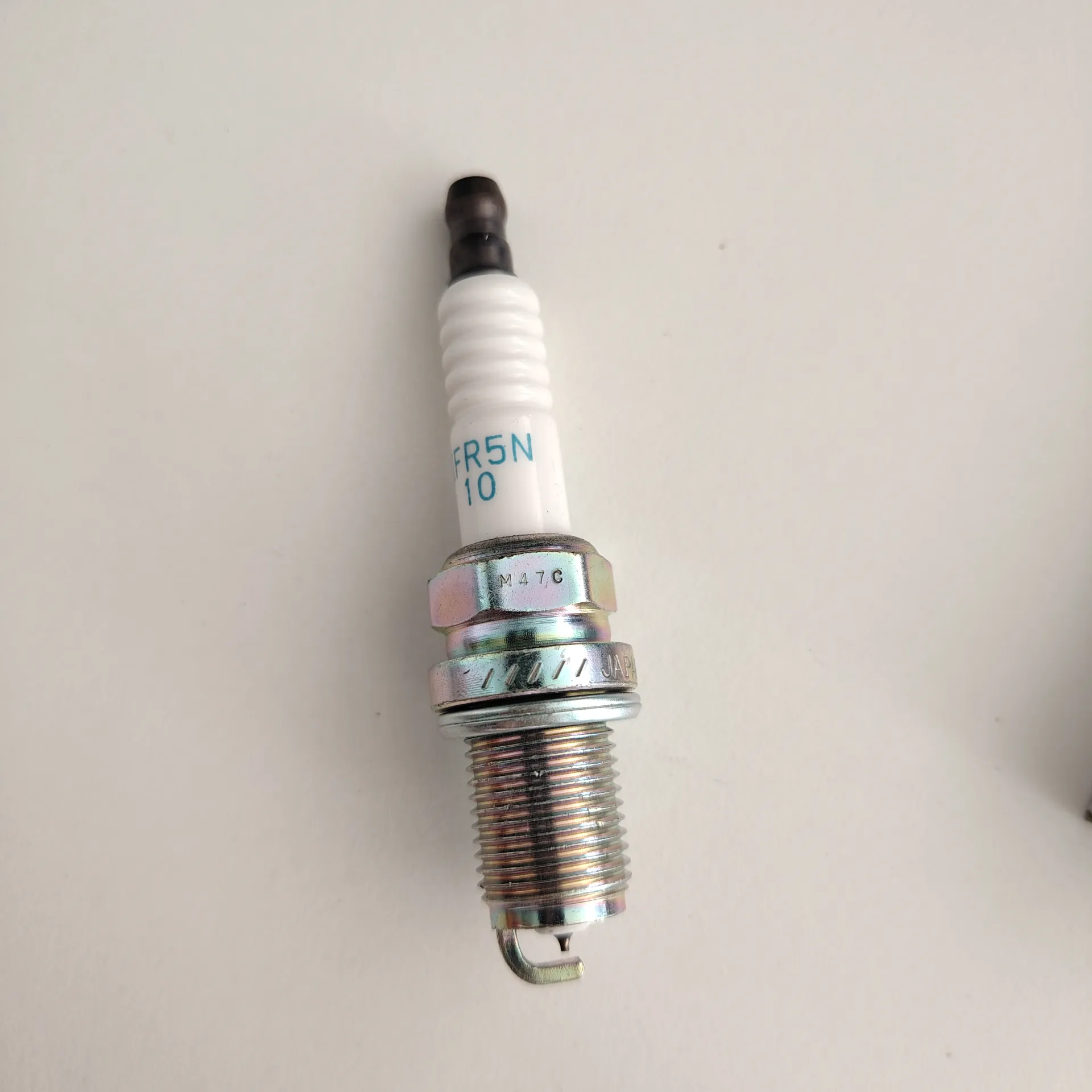
Drawing from years of experience in mechanical engineering and a thorough analysis of market demands, it’s evident that the importance of tiny rubber gaskets transcends simple sealing tasks. They are essential in preventing leaks, containing pressure, and ensuring safety across various applications, from automotive engines to household appliances and even in sensitive medical equipment.
One of the critical aspects contributing to the efficacy and reliability of rubber gaskets is the selection of material. Different rubber materials, including nitrile, silicone, neoprene, and EPDM, offer distinct advantages, such as resistance to temperature variations, chemical interactions, and environmental factors. For instance, silicone rubber gaskets are immensely popular in industries requiring high-temperature resistance, while nitrile rubber is preferred for applications involving oils and fuels. Expertise in selecting the appropriate material significantly enhances the functionality and longevity of the gasket, ensuring optimal performance under specific conditions.
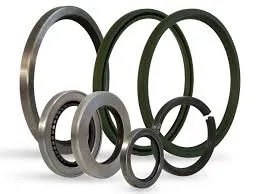
Manufacturers specializing in tiny rubber gaskets have honed their craft through years of dedication and technological advancements. Cutting-edge manufacturing processes, such as compression molding and injection molding, have revolutionized the industry. These techniques allow for intricate designs and precision-cut gaskets that cater to the increasingly complex needs of modern machinery. The move towards automation and computer-aided design in gasket production has also catapulted the quality and consistency of these products, further solidifying their indispensability.
tiny rubber gaskets
Authoritative discussions and comprehensive research studies often highlight the ongoing innovations within the rubber gasket industry. A notable development is the integration of environmental considerations into the manufacturing process. Eco-friendly initiatives, such as recycling rubber material and utilizing sustainable sources, are gaining momentum. This shift not only adheres to stricter environmental regulations but also underscores the industry's commitment to sustainability.
Trustworthiness in the gasket industry is paramount. Products undergo rigorous testing to meet industry standards, with attention to specifications such as tensile strength, compression set, and thermal stability. Accredited certifications and meticulously documented quality control procedures add layers of assurance to the integrity of rubber gaskets. Selecting a supplier with a robust track record and adherence to industry guidelines is essential to ensure that the gaskets will perform reliably in their designated applications.
Real-world applications and user experiences further emphasize the understated importance of tiny rubber gaskets. In automotive contexts, precise sealing can mean the difference between efficient engine performance and costly breakdowns. In the medical field, gaskets used in devices like ventilators must meet stringent hygiene standards while providing exceptional reliability to safeguard patient health. These scenarios highlight that while rubber gaskets are not visible frontline components, they are crucial enablers of function and safety.
In conclusion, tiny rubber gaskets epitomize the blend of traditional engineering expertise and modern technological advancements. They serve as silent custodians of safety and efficiency across diverse fields. An appreciation for their nuanced roles and a commitment to selecting high-quality materials and manufacturers can significantly enhance performance outcomes in any sector they are deployed. As industry needs continue to evolve, staying informed about advancements and maintaining rigorous standards remain integral to leveraging the full potential of these indispensable components.